Automobile seat cushion rear pipe cold forming technology
A car seat, cold forming technology, applied in the direction of vehicle parts, transportation and packaging, can solve the problems of the stamping die cannot be maintained in time, the state of the stamping is unstable, and the welding is not guaranteed, so as to achieve no welding fumes and improve production. Efficiency and equipment convenience
- Summary
- Abstract
- Description
- Claims
- Application Information
AI Technical Summary
Problems solved by technology
Method used
Image
Examples
example 1
[0036] Step 1. Start the forming mold equipment, which is in working state;
[0037] Step 2. Put the product to be processed into the first cavity of the forming mold, start the forming mold to radially extrude the product to form an axisymmetric groove, the radial extrusion of the mold is 6MPa, and keep 15MPa when the mold is completely closed The pressure is 1S, the processed product is low carbon steel, the thickness of the product pipe wall is 2.0mm, the axial length of the extruded product is 50mm, and the first process is completed after the product is extruded;
[0038] Step 3. Put the product extruded in the first process into the second cavity of the forming mold, start the forming mold to extrude the product axially, the axial extrusion of the mold is 6MPa, and maintain a pressure of 15MPa when the mold is completely closed 1S, when the upper and lower molds are in contact, the mold closing speed is 30mm / s, the axial length of the extruded product is 7mm, and the sec...
example 2
[0044] Step 1. Start the forming mold equipment, which is in working state;
[0045] Step 2. Put the product to be processed into the first cavity of the forming mold, start the forming mold to radially extrude the product to form an axisymmetric groove, the radial extrusion of the mold is 7MPa, and keep 15MPa when the mold is completely closed The pressure is 1S, the processed product is low carbon steel, the thickness of the product pipe wall is 2.2mm, the axial length of the extruded product is 50mm, and the first process is completed after the product is extruded;
[0046] Step 3. Put the product extruded in the first process into the second cavity of the forming mold, start the forming mold to extrude the product axially, the axial extrusion of the mold is 7MPa, and maintain a pressure of 15MPa when the mold is completely closed 1S, when the upper and lower molds are in contact, the mold closing speed is 30mm / s, the axial length of the extruded product is 9mm, and the sec...
PUM
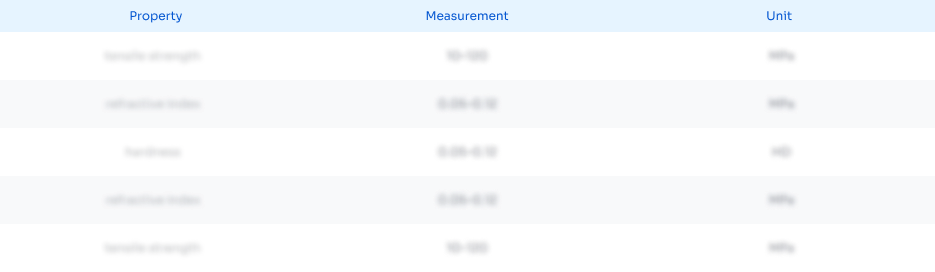
Abstract
Description
Claims
Application Information

- R&D
- Intellectual Property
- Life Sciences
- Materials
- Tech Scout
- Unparalleled Data Quality
- Higher Quality Content
- 60% Fewer Hallucinations
Browse by: Latest US Patents, China's latest patents, Technical Efficacy Thesaurus, Application Domain, Technology Topic, Popular Technical Reports.
© 2025 PatSnap. All rights reserved.Legal|Privacy policy|Modern Slavery Act Transparency Statement|Sitemap|About US| Contact US: help@patsnap.com