A co-rotating twin-screw transmission device using an oil motor
A transmission device and oil motor technology, applied in transmission devices, transmission device parts, gear transmission devices, etc., can solve the problems of large space occupation and complex structure
- Summary
- Abstract
- Description
- Claims
- Application Information
AI Technical Summary
Problems solved by technology
Method used
Image
Examples
Embodiment
[0019] A kind of co-rotating twin-screw transmission device adopting oil motor of the present invention, such as figure 1 , 2 As shown, including output gear shaft A1, output gear shaft B2, thrust roller bearing, transition gear shaft A4, input gear shaft A5, oil motor bracket, oil motor A7, thrust bearing, coupling, oil motor B11, transmission Case body 12, input gear shaft B13, transition gear shaft B14.
[0020] The output gear shaft A1 and the output gear shaft B2 are horizontally arranged in the center of the transmission box 12 in parallel, and transmission gears are fixed on the output gear shaft A1 and the output gear shaft B2, and the transmission gears on the output gear shaft A1 and the output gear shaft B2 are front and rear Dislocation setting; the rear ends of the output gear shaft A1 and the output gear shaft B2 both pass through the rear end of the transmission box 12, and are respectively connected with a set of thrust bearings, and the two sets of thrust bea...
PUM
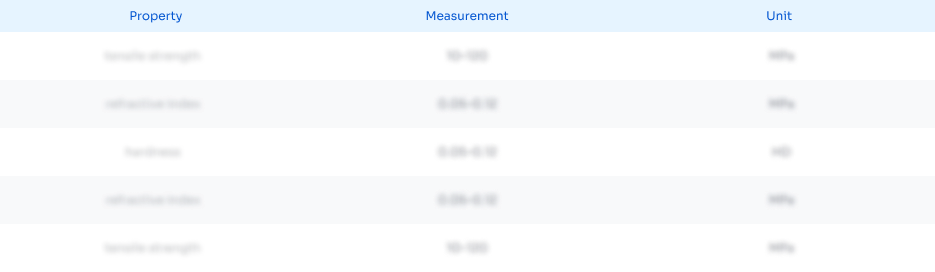
Abstract
Description
Claims
Application Information

- R&D
- Intellectual Property
- Life Sciences
- Materials
- Tech Scout
- Unparalleled Data Quality
- Higher Quality Content
- 60% Fewer Hallucinations
Browse by: Latest US Patents, China's latest patents, Technical Efficacy Thesaurus, Application Domain, Technology Topic, Popular Technical Reports.
© 2025 PatSnap. All rights reserved.Legal|Privacy policy|Modern Slavery Act Transparency Statement|Sitemap|About US| Contact US: help@patsnap.com