Numerical control welding method, numerical control welding device and numerical control welding system
A welding method and welding device technology, applied in auxiliary devices, welding equipment, auxiliary welding equipment, etc., can solve the problems of low welding efficiency, irregular tooling, labor intensity of workers, etc., and achieve accurate positioning of welding points and welding tracking. The effect of accurate and high-efficiency automatic welding
- Summary
- Abstract
- Description
- Claims
- Application Information
AI Technical Summary
Problems solved by technology
Method used
Image
Examples
Embodiment Construction
[0027] The present invention will be described in further detail below through specific implementation examples and in conjunction with the accompanying drawings.
[0028] see figure 1 , the embodiment of the present invention provides a kind of numerical control welding method, comprises the following steps:
[0029] Step S100, pre-collecting the video image of the preset weld position, performing edge sharpening processing, and obtaining the sharpened image of the preset weld position after the edge is enhanced;
[0030] Step S200, focus the camera on the welding head on the welding torch, and collect a video image containing the welding head and the current welding seam position each time the camera is adjusted to capture a new position, perform edge sharpening processing, and obtain the enhanced edge containing A sharpened image of the weld head and the current weld position;
[0031] Step S300, judging whether the sharpened image containing the welding head and the curr...
PUM
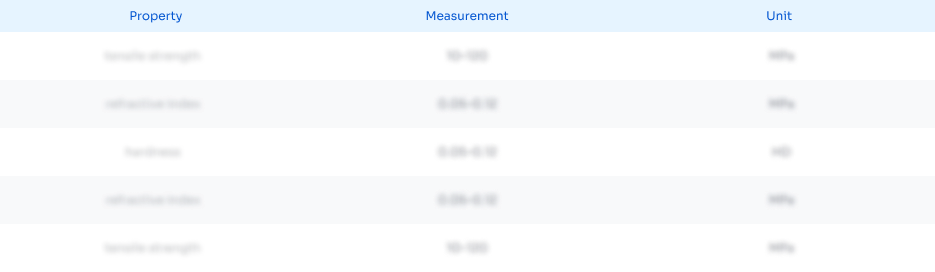
Abstract
Description
Claims
Application Information

- R&D
- Intellectual Property
- Life Sciences
- Materials
- Tech Scout
- Unparalleled Data Quality
- Higher Quality Content
- 60% Fewer Hallucinations
Browse by: Latest US Patents, China's latest patents, Technical Efficacy Thesaurus, Application Domain, Technology Topic, Popular Technical Reports.
© 2025 PatSnap. All rights reserved.Legal|Privacy policy|Modern Slavery Act Transparency Statement|Sitemap|About US| Contact US: help@patsnap.com