Method for eliminating undercut of involute gear
A technology of involute gears and involutes, applied to components with teeth, belts/chains/gears, portable lifting devices, etc., can solve the problem of reduced coincidence, inability to reduce or eliminate defects of involute gears, Reduce transmission accuracy and other issues
- Summary
- Abstract
- Description
- Claims
- Application Information
AI Technical Summary
Problems solved by technology
Method used
Image
Examples
Embodiment approach 1
[0054] Embodiment 1: In this embodiment, the method for eliminating the undercut of the involute gear firstly calculates the minimum number of teeth for which the involute gear does not undercut:
[0055] When processing standard spur involute cylindrical gears, the modulus m is 5, , and , the minimum number of teeth without undercutting is:
[0056]
[0057] When machining standard helical involute cylindrical gears, , , and , the minimum number of teeth without undercutting is:
[0058]
[0059] When machining standard spur involute bevel gears, due to the head clearance coefficient Set to 0.2. Equivalent of involute bevel gear Minimum number of teeth of straight involute cylindrical gear , when , , by the formula:
[0060]
[0061] Then the minimum number of teeth of the standard involute spur bevel gear without undercutting for:
[0062]
[0063] in, , .
[0064] After calculation, the data are shown in Table 1.
[0065] Table 1 ...
Embodiment approach 2
[0068] Embodiment 2: In this embodiment, the method for eliminating the undercut of the involute gear first calculates the minimum number of teeth for which the involute gear does not undercut:
[0069] When processing short-toothed involute spur gears, the modulus m is 5, , and , the minimum number of teeth without undercutting is:
[0070]
[0071] When machining short-toothed involute helical cylindrical gears, , , and , the minimum number of teeth without undercutting is:
[0072]
[0073] When machining short-toothed involute straight bevel gears, due to the top clearance coefficient Set to 0.2. The equivalent of the involute bevel gear, the minimum number of teeth of the involute spur gear without undercutting is equal to ,at this time , , by the formula:
[0074]
[0075] Then the minimum number of teeth of the short-toothed involute spur bevel gear without undercutting for:
[0076]
[0077] in, , .
[0078] After calculation,...
Embodiment approach 3
[0082] Embodiment 3: In this embodiment, the method for eliminating undercutting of involute gears firstly calculates the minimum number of teeth of involute gears without undercutting:
[0083] For involute gears with pressure angles of 14.5°, 22.5°, and 25°:
[0084] When processing straight involute cylindrical gears, the modulus m is 5, , and , the minimum number of teeth without undercutting is:
[0085]
[0086] When machining helical involute cylindrical gears, , , and , the minimum number of teeth without undercutting is:
[0087]
[0088] When machining straight involute bevel gears, due to the head clearance coefficient Set to 0.2. Equivalent of involute bevel gear Minimum number of teeth of involute spur gear ,at this time , , by the formula:
[0089]
[0090] Then the minimum number of teeth of straight involute bevel gear without undercutting for:
[0091]
[0092] in, , .
[0093] After calculation, the data are shown ...
PUM
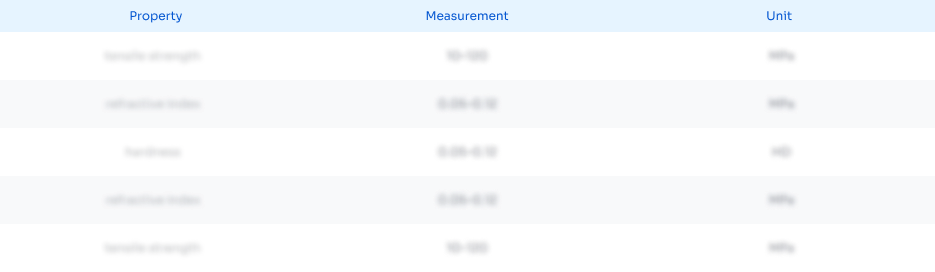
Abstract
Description
Claims
Application Information

- R&D
- Intellectual Property
- Life Sciences
- Materials
- Tech Scout
- Unparalleled Data Quality
- Higher Quality Content
- 60% Fewer Hallucinations
Browse by: Latest US Patents, China's latest patents, Technical Efficacy Thesaurus, Application Domain, Technology Topic, Popular Technical Reports.
© 2025 PatSnap. All rights reserved.Legal|Privacy policy|Modern Slavery Act Transparency Statement|Sitemap|About US| Contact US: help@patsnap.com