Embedded integrated intelligent die
An embedded and mold technology, applied in the direction of forming tools, manufacturing tools, presses, etc., can solve the problems of speed, acceleration and pressure that cannot be directly obtained, repeated mold adjustments, and inability to fully fit, etc., to reduce mold debugging time and reduce The effect of defective rate, convenient and timely maintenance
- Summary
- Abstract
- Description
- Claims
- Application Information
AI Technical Summary
Problems solved by technology
Method used
Image
Examples
Embodiment 2
[0034] Embodiment 2: The difference between this embodiment and the above embodiment 1 is that: the die 5 is also provided with a pressure sensor 50 . The pressure sensor 50 adopts a strain gauge pressure sensor, and a strain gauge is provided on the side wall of the die 5 to calculate the pressure on the die during the stamping process by sensing the deformation of the side wall of the die 5, thereby realizing When the mold is reproduced, the data control center automatically adjusts the pressure through the stored data, and at the same time during the processing and production process, the data control center uses the strain gauge to record each pressure in the stamping process to obtain the number of times the mold is used, and then This data is checked against the pre-set mold maintenance frequency to prompt mold maintenance.
Embodiment 3
[0035] Embodiment 3: This embodiment monitors the punching process of the mold in real time. The difference between Embodiment 3 and the above embodiment 2 is that a temperature sensor is embedded in the punch, and the temperature sensor is embedded in the punch and the die. In the vicinity of the contact point, the temperature sensor is used to monitor the real-time temperature of the punch and die during the mold punching process, supervise the mold, and sense the corresponding vulnerable points of the mold. When the actual temperature exceeds a certain theoretical safety value At this time, the stamping operation can be stopped through the data control center, and the position of the vulnerable point of the mold can be prompted and given a warning through display equipment, sound and light alarms, etc.
Embodiment 4
[0036] Embodiment 4: The difference between this embodiment and Embodiment 3 is that a displacement sensor 60 is also provided on the upper end surface of the lower formwork plate 6 . Measure the pressing height of the upper mold base plate 1 during each stamping process by setting a displacement sensor 60 on the upper end surface of the lower mold base plate 6, and transmit the measured data to the data control center for memory storage, so that when When the mold is used on other different punching machines, the punching machine can automatically adjust the stroke through the data stored in the mold, so as to realize the automatic adjustment of the closing height of the mold, so that the adjustment and use of the mold will not be affected by the change of the punching machine, and avoid repeated debugging of the mold. Save costs and greatly improve work efficiency.
PUM
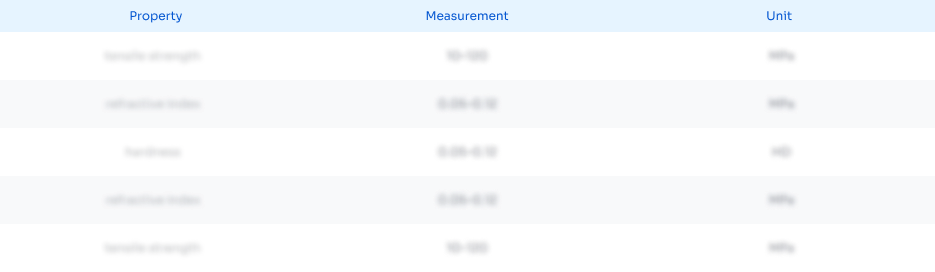
Abstract
Description
Claims
Application Information

- Generate Ideas
- Intellectual Property
- Life Sciences
- Materials
- Tech Scout
- Unparalleled Data Quality
- Higher Quality Content
- 60% Fewer Hallucinations
Browse by: Latest US Patents, China's latest patents, Technical Efficacy Thesaurus, Application Domain, Technology Topic, Popular Technical Reports.
© 2025 PatSnap. All rights reserved.Legal|Privacy policy|Modern Slavery Act Transparency Statement|Sitemap|About US| Contact US: help@patsnap.com