Finishing rolling method and device of oblique axial rolling cored steel
A longitudinal rolling and hollow technology, applied in the direction of metal rolling, etc., can solve the problems of inner hole quality defects, slow final rolling speed, irregular shape, etc., to eliminate cross-rolling spiral traces, avoid retention and existence, and improve appearance The effect of the surface state
- Summary
- Abstract
- Description
- Claims
- Application Information
AI Technical Summary
Problems solved by technology
Method used
Image
Examples
Embodiment Construction
[0025] The present invention will be further described in detail below in conjunction with the accompanying drawings and embodiments.
[0026] Embodiments of the present invention: the finishing rolling method of a kind of oblique longitudinal rolling hollow steel of the present invention can be implemented as the final rolling process in the existing oblique longitudinal rolling hollow steel process. When implementing, first adopt the existing oblique longitudinal rolling Process The raw material billet for making hollow steel is subjected to cross-rolling piercing rolling, cored (rod) cross-rolling pipe rolling, and second coreless (rod) cross-rolling pipe sizing rolling to obtain a hot pipe billet, and then adopts this method The invented method carries out the final rolling of the hot tube billet. When the hot tube billet is finished rolling, the hot tube billet is continuously rolled by setting two groups of roll groups on a Y-shaped rolling mill. Each group of roll groups...
PUM
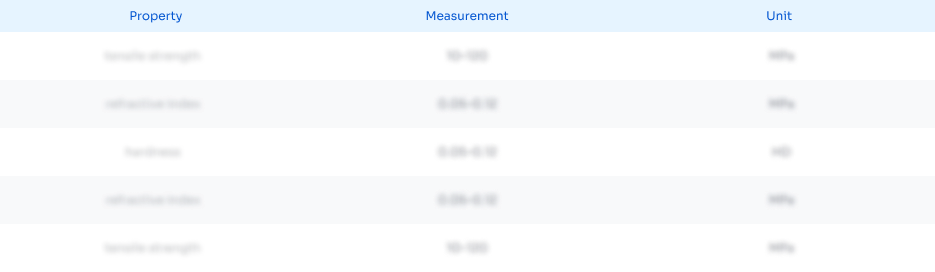
Abstract
Description
Claims
Application Information

- Generate Ideas
- Intellectual Property
- Life Sciences
- Materials
- Tech Scout
- Unparalleled Data Quality
- Higher Quality Content
- 60% Fewer Hallucinations
Browse by: Latest US Patents, China's latest patents, Technical Efficacy Thesaurus, Application Domain, Technology Topic, Popular Technical Reports.
© 2025 PatSnap. All rights reserved.Legal|Privacy policy|Modern Slavery Act Transparency Statement|Sitemap|About US| Contact US: help@patsnap.com