Numerically simulating structural behaviors of a product by using explicit finite element analysis with a combined technique of mass scaling and subcycling
A finite element and mass technology, which is applied in the field of computer-aided engineering analysis and can solve problems such as changing the dynamic performance of structures
- Summary
- Abstract
- Description
- Claims
- Application Information
AI Technical Summary
Problems solved by technology
Method used
Image
Examples
Embodiment Construction
[0024] figure 1 is a flowchart illustrating an exemplary process 100 for numerically simulating the structural performance of a product using explicit finite element analysis (FEA), employing a combined technique of subcycles and mass scaling, in accordance with an embodiment of the present invention. Preferably, process 100 is understood in conjunction with other diagrams and is implemented in software.
[0025] Process 100 begins by receiving a finite element analysis (FEA) model representing a product or structure (eg, automobile, aircraft, etc.) at step 102 . The FEA model includes a number of nodes and a number of finite elements defining the product, with associated material properties. Types of finite elements may include but are not limited to solids, shells, harnesses, truss, etc. ( Figure 4 An exemplary shell element 401 and an exemplary solid element 402 are shown). In addition, the minimum time step (Δt min ) (for example, by users (i.e. engineers, scientists ...
PUM
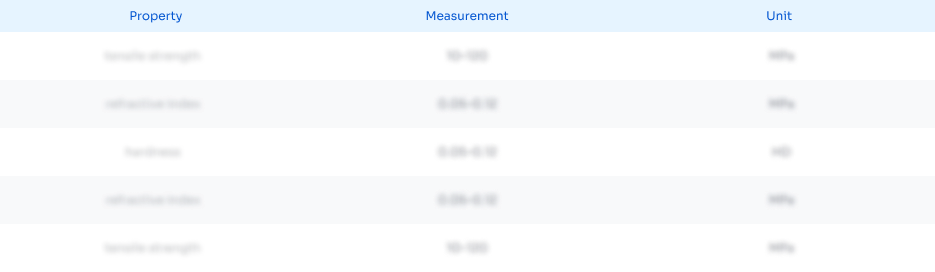
Abstract
Description
Claims
Application Information

- R&D
- Intellectual Property
- Life Sciences
- Materials
- Tech Scout
- Unparalleled Data Quality
- Higher Quality Content
- 60% Fewer Hallucinations
Browse by: Latest US Patents, China's latest patents, Technical Efficacy Thesaurus, Application Domain, Technology Topic, Popular Technical Reports.
© 2025 PatSnap. All rights reserved.Legal|Privacy policy|Modern Slavery Act Transparency Statement|Sitemap|About US| Contact US: help@patsnap.com