Yoga mat making method
A technology of yoga mats and elastomers, applied in the field of materials, can solve the problems of short service life of yoga mats, poor elasticity of yoga mats, poor anti-slip effect, etc., and achieve the effects of light weight, good environmental protection performance, and portability
- Summary
- Abstract
- Description
- Claims
- Application Information
AI Technical Summary
Problems solved by technology
Method used
Examples
Embodiment 1
[0021] The elastomer used is styrene thermoplastic elastomer (SBS), and its weight portion is 20 parts; The nylon used is polyhexamethylene adipate, and its weight portion is 50 parts; The weight portion of polyvinyl alcohol resin is 50 parts. share. Its parts by weight of naphthenic oil used are 10 parts; The antioxidant used is tetrakis [beta-(3,5-di-tert-butyl-4-hydroxyphenyl) propionate] pentaerythritol ester, and its parts by weight are 0.1 parts; used softening agent is calcium stearate, and its parts by weight are 5 parts.
[0022] Then put the material into a blender and stir for 3 minutes. After stirring evenly, put it into an injection molding machine for injection molding at a temperature of 180°C for 2 minutes, then pour it into a mold, and mold it into a yoga mat at a temperature of 20°C.
Embodiment 2
[0024] The elastomer used is styrene-based thermoplastic elastomer (SBS), and its weight part is 30 parts; the nylon used is polycaprolactam, and its weight part is 40 parts; the weight part of polyvinyl alcohol resin is 60 parts. Its parts by weight of naphthenic oil used are 15 parts; The antioxidant used is tetrakis [β-(3,5-di-tert-butyl-4-hydroxyphenyl) propionate] pentaerythritol ester, and its parts by weight are 0.8 Parts; The softening agent used is pine oil, and its parts by weight are 8 parts.
[0025] Then put the material into a blender and stir for 4 minutes. After stirring evenly, put it into an injection molding machine for injection molding at a temperature of 200°C for 3 minutes, then pour it into a mold, and mold it into a yoga mat at a temperature of 30°C.
Embodiment 3
[0027] The elastomer used is thermoplastic elastomer (POE), and its weight part is 30 parts; The nylon used is polybutylene adipate, and its weight part is 30 parts; The weight part of polyvinyl alcohol resin is 40 parts. Its parts by weight of naphthenic oil used are 12 parts; The antioxidant used is β-(3,5-di-tert-butyl-4-hydroxyl phenyl) n-octadecyl propionate, and its parts by weight are 0.4 parts by weight. Parts; The softening agent used is dioctyl phthalate, and its parts by weight are 10 parts.
[0028] Then put the material into a blender and stir for 5 minutes. After stirring evenly, put it into an injection molding machine for injection molding at a temperature of 195°C for 3 minutes, then pour it into a mold, and mold it into a yoga mat at a temperature of 40°C.
PUM
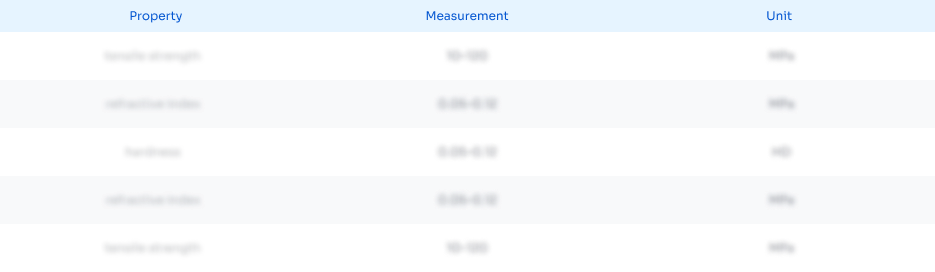
Abstract
Description
Claims
Application Information

- R&D
- Intellectual Property
- Life Sciences
- Materials
- Tech Scout
- Unparalleled Data Quality
- Higher Quality Content
- 60% Fewer Hallucinations
Browse by: Latest US Patents, China's latest patents, Technical Efficacy Thesaurus, Application Domain, Technology Topic, Popular Technical Reports.
© 2025 PatSnap. All rights reserved.Legal|Privacy policy|Modern Slavery Act Transparency Statement|Sitemap|About US| Contact US: help@patsnap.com