Improved Delta parallel mechanism robot
A robot and an improved technology, applied in manipulators, program-controlled manipulators, manufacturing tools, etc., can solve the problems of Delta robots, such as increased cost of transportation, reduced working range of motion, and large impact of vibration, to achieve volume and mass reduction. , Grabbing accuracy is improved, and the effect of ensuring stability
- Summary
- Abstract
- Description
- Claims
- Application Information
AI Technical Summary
Problems solved by technology
Method used
Image
Examples
Embodiment Construction
[0019] Specific embodiments of the present invention will be further described below in conjunction with the accompanying drawings.
[0020] An improved Delta parallel mechanism robot, its structure is as follows:
[0021] Mechanical part: three sets of electric linear guide rails, stepping motor, parallelogram branch chain, ball joint, moving platform, aluminum profile. The electric linear guide adopts the German Festo electric linear guide with a stroke of 300mm. The stepper motor adopts Sanyo stepper motor,
[0022] control part (such as image 3 ): high-speed motion control module, stepper motor driver, power supply.
[0023] An improved Delta parallel robot of the present invention adopts three Beckhoff high-speed motion control modules EL2521-0024 and an input module EL1088, and adopts a Sanyo stepping motor driver.
[0024] When an improved Delta parallel robot of the present invention is working, the control program is written by the soft PLC software CoDeSys of th...
PUM
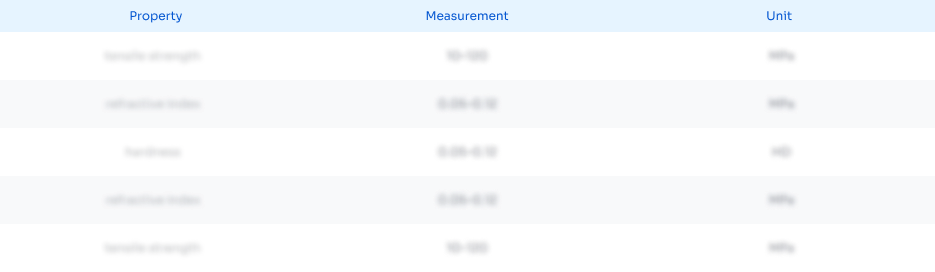
Abstract
Description
Claims
Application Information

- R&D
- Intellectual Property
- Life Sciences
- Materials
- Tech Scout
- Unparalleled Data Quality
- Higher Quality Content
- 60% Fewer Hallucinations
Browse by: Latest US Patents, China's latest patents, Technical Efficacy Thesaurus, Application Domain, Technology Topic, Popular Technical Reports.
© 2025 PatSnap. All rights reserved.Legal|Privacy policy|Modern Slavery Act Transparency Statement|Sitemap|About US| Contact US: help@patsnap.com