Method for calibrating center line of guide ruler
A technology of center line and guide ruler, which is applied in the directions of guiding/positioning/alignment devices, metal rolling, manufacturing tools, etc. The problem of residual steel scraps on the ruler liner can be avoided, so as to avoid one-side wear of the guide ruler, reduce unqualified products, and save grinding time
- Summary
- Abstract
- Description
- Claims
- Application Information
AI Technical Summary
Problems solved by technology
Method used
Image
Examples
Embodiment Construction
[0018] The specific embodiment of the present invention will be further described below in conjunction with accompanying drawing:
[0019] See figure 1 , is a structural schematic diagram of an embodiment of a method for calibrating the centerline of the guide rail according to the present invention. Under normal circumstances, calibration is performed after each overhaul. Since the guide rail is easily deflected when the strip steel is rolled over 18mm, it is therefore easy to roll over 18mm. After the steel is stripped, the offset of the guide ruler relative to the transmission side and the working side should be corrected in time to ensure the centering of the guide ruler 1. The specific operation steps are as follows:
[0020] 1) Measure the width L of the extension strip 2 in the middle of the guide ruler, the distance L2 between the edge of the extension strip 2 driving side and the guide plate 3 on the transmission side, the distance L1 between the edge of the extension...
PUM
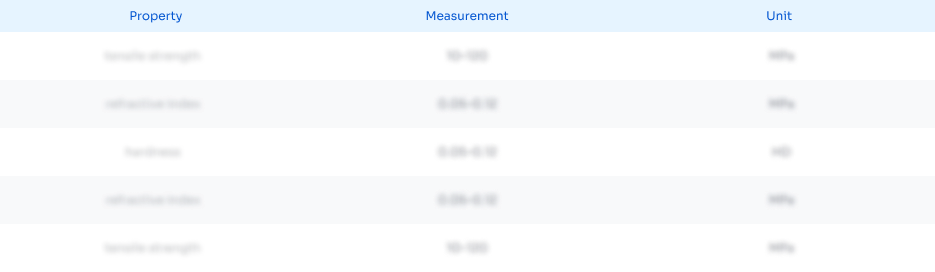
Abstract
Description
Claims
Application Information

- Generate Ideas
- Intellectual Property
- Life Sciences
- Materials
- Tech Scout
- Unparalleled Data Quality
- Higher Quality Content
- 60% Fewer Hallucinations
Browse by: Latest US Patents, China's latest patents, Technical Efficacy Thesaurus, Application Domain, Technology Topic, Popular Technical Reports.
© 2025 PatSnap. All rights reserved.Legal|Privacy policy|Modern Slavery Act Transparency Statement|Sitemap|About US| Contact US: help@patsnap.com