Electromagnetic friction stir spot welding device and method thereof
An electromagnetic stirring and friction point technology, which is applied in non-electric welding equipment, welding equipment, metal processing equipment, etc., can solve the problems of unsatisfactory degree of recrystallization structure refinement, withdrawing from the concave hole, and exiting the concave hole in the existing process. The effect of improving the microstructure, improving the plastic flow ability and improving the overall quality
- Summary
- Abstract
- Description
- Claims
- Application Information
AI Technical Summary
Problems solved by technology
Method used
Image
Examples
Embodiment Construction
[0025] In order to describe in detail the technical content, structural features, achieved objectives and effects of the present invention, the following will be described in detail in conjunction with embodiments and accompanying drawings.
[0026] See figure 1 , figure 1 Shown is the structural schematic diagram of the electromagnetic friction stir spot welding device of the present invention. The electromagnetic friction stir spot welding device 1 includes a welding pad 11, the welding pad 11 is used to carry the plate 2 to be welded; a stirring head 12, the stirring head 12 is used to weld the plate 2 to be welded, And further includes a stirring needle 121 arranged in the inner layer of the stirring head 12, a clamping sleeve 122 arranged on the outer layer of the stirring head 12, and a stirring needle 121 and the clamping sleeve 122 arranged between The stirring sleeve 123, the stirring needle 121, the stirring sleeve 123, and the clamping sleeve 122 are arranged on the sa...
PUM
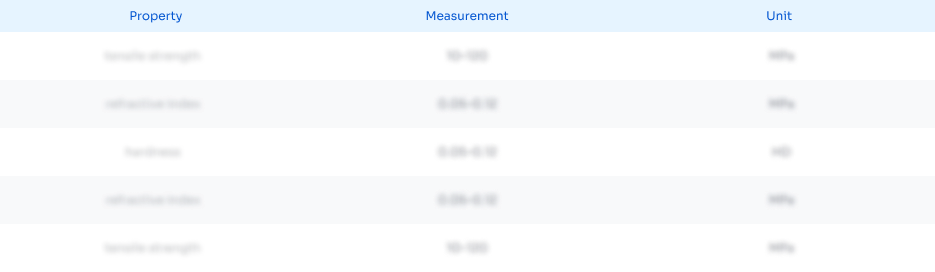
Abstract
Description
Claims
Application Information

- R&D Engineer
- R&D Manager
- IP Professional
- Industry Leading Data Capabilities
- Powerful AI technology
- Patent DNA Extraction
Browse by: Latest US Patents, China's latest patents, Technical Efficacy Thesaurus, Application Domain, Technology Topic, Popular Technical Reports.
© 2024 PatSnap. All rights reserved.Legal|Privacy policy|Modern Slavery Act Transparency Statement|Sitemap|About US| Contact US: help@patsnap.com