Beta-semi-hydrated gypsum powder calcination preparation technique and calcination apparatus
A preparation process, the technology of hemihydrate gypsum, which is applied in the field of gypsum powder production, can solve the problems of non-compliance with national environmental protection regulations, large size of the kiln body in the longitudinal direction, and high cost of heat exchange oil, so as to ensure the calcination time, normal settlement, The effect of basic area saving
- Summary
- Abstract
- Description
- Claims
- Application Information
AI Technical Summary
Problems solved by technology
Method used
Image
Examples
Embodiment Construction
[0022] The present invention will be described in detail below in conjunction with the drawings. A calcination preparation process of β-type hemihydrate gypsum powder, characterized in that: the preparation process includes the following steps:
[0023] 1) Crush the raw materials into 100-140 mesh size powder;
[0024] 2) The powder particles are transported into the rotary kiln through the inlet of the calcining equipment for calcination, and then continuously output from the outlet of the calcining equipment after passing at least two concentric rotating drums. The kiln head temperature is 450-550 ℃, kiln tail temperature is 155-190℃, powder temperature is 150-185℃.
[0025] In order to achieve the purpose of saving floor space and improving heat utilization efficiency, there are three concentric drums in this equipment, namely the inner drum 8, the intermediate drum 7 and the outer drum 6. The powder particles are axially in the three concentric drums. The speed is different. W...
PUM
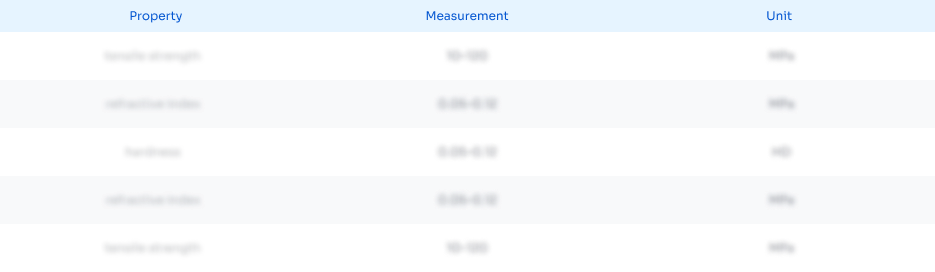
Abstract
Description
Claims
Application Information

- R&D
- Intellectual Property
- Life Sciences
- Materials
- Tech Scout
- Unparalleled Data Quality
- Higher Quality Content
- 60% Fewer Hallucinations
Browse by: Latest US Patents, China's latest patents, Technical Efficacy Thesaurus, Application Domain, Technology Topic, Popular Technical Reports.
© 2025 PatSnap. All rights reserved.Legal|Privacy policy|Modern Slavery Act Transparency Statement|Sitemap|About US| Contact US: help@patsnap.com