Device for producing crystal glass
A crystal glass and blast furnace technology, which is applied in glass forming, glass production, glass manufacturing equipment, etc., can solve the problems of operator injury, low production efficiency, high product cost, etc., to reduce energy consumption, improve production efficiency, and reduce defective products. The effect of yield reduction
- Summary
- Abstract
- Description
- Claims
- Application Information
AI Technical Summary
Problems solved by technology
Method used
Image
Examples
Embodiment 1
[0044] Such as figure 1 As shown, the blast furnace mainly includes a chemical tank 1, a clarification tank 2, a working room 3, a discharge tank 4, and a heating rod 26;
[0045] The heating rod 26 is placed in the chemical tank 1, and the heating rod 26 is connected to the power controller of the blast furnace through a wire; the chemical tank 1, the clarification tank 2, the working room 3, and the discharge tank 4 of the blast furnace are connected in sequence, and the middle is designed with The connection channel is designed with a discharge port 5 at the lower end of the discharge pool 4, and the discharge port 5 corresponds to the upper end of the guide groove 8 of the molding device;
[0046] Chemical tank 1, clarifying tank 2, working room 3, and discharging tank 4 are designed as a square structure, which is made of refractory materials. 20-30cm lower;
[0047] The chemical tank 1 is designed to be open to monitor the reaction of the material, and the clarifier 2,...
Embodiment 2
[0060] Such as figure 1 As shown, the blast furnace mainly includes a chemical tank 1, a clarification tank 2, a working room 3, a discharge tank 4, and a heating rod 26;
[0061] The heating rod 26 is placed in the chemical tank 1, and the heating rod 26 is connected to the power controller of the blast furnace through a wire; the chemical tank 1, the clarification tank 2, the working room 3, and the discharge tank 4 of the blast furnace are connected in sequence, and the middle is designed with The connection channel is designed with a discharge port 5 at the lower end of the discharge pool 4, and the discharge port 5 corresponds to the upper end of the guide groove 8 of the molding device;
[0062] Chemical tank 1, clarifying tank 2, working room 3, and discharging tank 4 are designed as polygonal structures made of refractory materials. 40-50cm lower;
[0063] The chemical tank 1 is designed to be open to monitor the reaction of the material, and the clarifier 2, the wor...
Embodiment 3
[0075] Embodiment three is the best embodiment;
[0076] Such as figure 1 As shown, the blast furnace mainly includes a chemical tank 1, a clarification tank 2, a working room 3, a discharge tank 4, and a heating rod 26;
[0077] The heating rod 26 is placed in the chemical tank 1, and the heating rod 26 is connected to the power controller of the blast furnace through a wire; the chemical tank 1, the clarification tank 2, the working room 3, and the discharge tank 4 of the blast furnace are connected in sequence, and the middle is designed with The connection channel is designed with a discharge port 5 at the lower end of the discharge pool 4, and the discharge port 5 corresponds to the upper end of the guide groove 8 of the molding device;
[0078] The chemical tank 1 and working room 3 are designed as polygonal shapes, and the clarification tank 2 and discharge tank 4 are designed as square structures, which are made of refractory materials. The lower end of pool 4 is 30-...
PUM
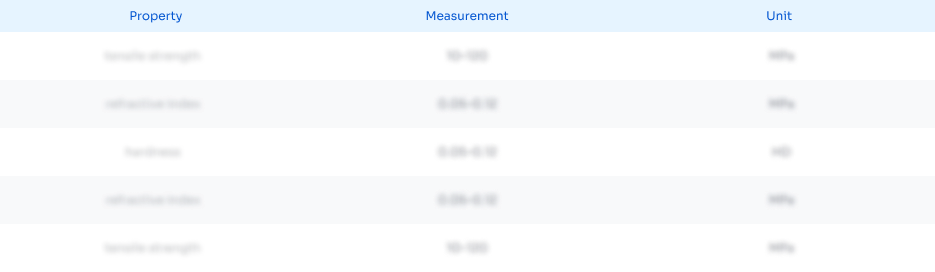
Abstract
Description
Claims
Application Information

- R&D
- Intellectual Property
- Life Sciences
- Materials
- Tech Scout
- Unparalleled Data Quality
- Higher Quality Content
- 60% Fewer Hallucinations
Browse by: Latest US Patents, China's latest patents, Technical Efficacy Thesaurus, Application Domain, Technology Topic, Popular Technical Reports.
© 2025 PatSnap. All rights reserved.Legal|Privacy policy|Modern Slavery Act Transparency Statement|Sitemap|About US| Contact US: help@patsnap.com