Process of rolling stainless steel coil in conventional hot continuous rolling production line
A technology of stainless steel and hot continuous rolling, which is applied in metal rolling, manufacturing tools, metal rolling, etc. It can solve the problems of stainless steel scratches, large rolling force, and large temperature difference between head and tail, and achieve the effect of saving production costs
- Summary
- Abstract
- Description
- Claims
- Application Information
AI Technical Summary
Problems solved by technology
Method used
Examples
Embodiment 1
[0021] The stainless steel slab with a thickness of 150㎜ is cold-packed into the walking beam heating furnace. The burners in the preheating section are all closed. The stainless steel slab is in the furnace for 200 minutes. Scaling machine descaling, open the header on the roughing descaling machine, the water outlet pressure is 18MPa, after the slab is descaled, it will be rolled in the roughing mill for 5 consecutive passes to form an intermediate slab with a thickness of 30mm, and the final roughing rolling temperature is 1070℃ , the intermediate billet enters the hot coil box through the intermediate roller table and is uncoiled. After the uncoiled intermediate billet passes through the flying shear head, it is sent to the finishing descaling machine. One of the headers of the finishing descaling machine is opened, and the outlet water pressure is 18MPa. After finishing and descaling, the intermediate billet enters the finishing tandem rolling unit with seven stands and ...
Embodiment 2
[0023] The 250mm thick stainless steel slab is cold loaded into the walking beam heating furnace. The burners in the preheating section are all closed. The stainless steel slab is in the furnace for 300 minutes. Scaling machine descaling, open the header on the roughing descaling machine, the water outlet pressure is 20MPa, after the slab is descaled, it will be rolled in the roughing mill for 7 consecutive passes to form an intermediate slab with a thickness of 35mm, and the roughing final rolling temperature is 1100℃ , the intermediate billet enters the hot coil box through the intermediate roller table and is uncoiled. After the uncoiled intermediate billet passes through the flying shear head, it is sent to the finishing descaling machine. One of the headers of the finishing descaling machine is opened. The scaled intermediate slab enters the finishing rolling mill with seven stands to be rolled into strip steel with a thickness of 3.5mm. The final rolling temperature of ...
Embodiment 3
[0025] Cold pack a stainless steel slab with a thickness of 200mm into a walking beam heating furnace. The burners in the preheating section of the heating furnace are all closed. The stainless steel slab is in the furnace for 250 minutes. When the stainless steel slab reaches the target temperature of 1250°C Out of the furnace, the stainless steel slab after being out of the furnace enters the rough rolling and descaling machine, and the header on the rough rolling and descaling machine is opened, and the outlet water pressure is 19MPa. The stainless steel slab (coarse) is descaled and then advanced to the rough rolling mill for 6 consecutive passes to be rolled into an intermediate slab with a thickness of 35mm. The final rolling temperature of the rough rolling is 1150°C. The intermediate billet passes through the intermediate roller table, passes through the flying shear head, and then is sent to the finish rolling and descaling machine. One of the headers of the finishin...
PUM
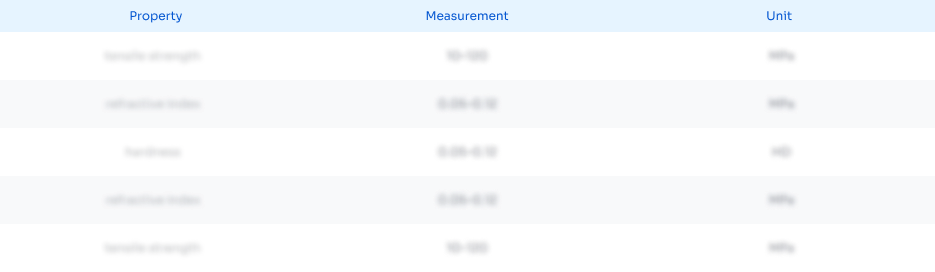
Abstract
Description
Claims
Application Information

- R&D
- Intellectual Property
- Life Sciences
- Materials
- Tech Scout
- Unparalleled Data Quality
- Higher Quality Content
- 60% Fewer Hallucinations
Browse by: Latest US Patents, China's latest patents, Technical Efficacy Thesaurus, Application Domain, Technology Topic, Popular Technical Reports.
© 2025 PatSnap. All rights reserved.Legal|Privacy policy|Modern Slavery Act Transparency Statement|Sitemap|About US| Contact US: help@patsnap.com