Electro-hydraulic power steering system for battery electric buses
A hydraulic power steering, pure electric technology, applied in the direction of electric steering mechanism, fluid steering mechanism, etc., can solve the problems of limited steering energy saving performance, no consideration of front axle load, no help for steering energy consumption, etc., to improve steering energy saving performance , Satisfying lightness and feel, taking into account the effect of stability and quick response performance
- Summary
- Abstract
- Description
- Claims
- Application Information
AI Technical Summary
Problems solved by technology
Method used
Image
Examples
Embodiment Construction
[0008] The specific content of the present invention will be described in detail below in conjunction with the accompanying drawings and specific embodiments.
[0009] like figure 1 As shown, the electrohydraulic power steering system of pure electric buses includes: steering wheel 1, steering oil tank 2, flow control valve and overflow valve assembly 3, steering hydraulic pump 4, steering drive three-phase asynchronous motor 6, frequency conversion 7, composite power supply 8, steering drive motor speed sensor 9, vehicle drive motor speed sensor 10, front axle load sensor 11, vehicle speed sensor 12 and recirculating ball integrated power steering device 14, the recirculating ball integrated power steering The device 14 is composed of a steering screw 15, a steering control valve 16, a steering power cylinder 17, a steering nut 18 and a steering gear fan 19. The steering wheel 1 is connected with the steering control valve 16 through the steering screw 15. A steering wheel a...
PUM
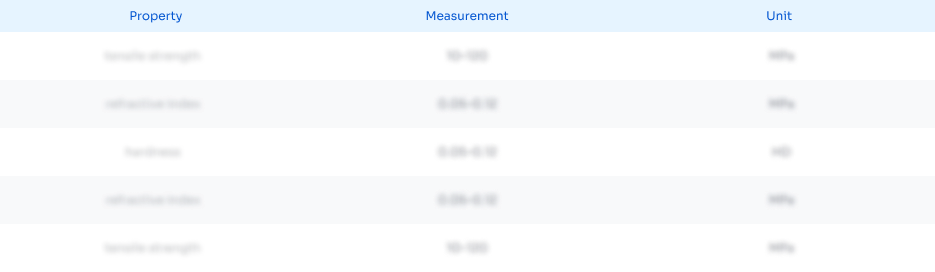
Abstract
Description
Claims
Application Information

- R&D Engineer
- R&D Manager
- IP Professional
- Industry Leading Data Capabilities
- Powerful AI technology
- Patent DNA Extraction
Browse by: Latest US Patents, China's latest patents, Technical Efficacy Thesaurus, Application Domain, Technology Topic, Popular Technical Reports.
© 2024 PatSnap. All rights reserved.Legal|Privacy policy|Modern Slavery Act Transparency Statement|Sitemap|About US| Contact US: help@patsnap.com