Manufacturing method of melamine ecological plate
A technology of melamine and its production method, which is applied to the jointing of wooden veneers, manufacturing tools, wood processing appliances, etc., can solve the problems of high aldehyde content, increased energy consumption, environmental pollution, etc., so as to reduce formaldehyde content and reduce production Effect of energy consumption and energy cost saving
- Summary
- Abstract
- Description
- Claims
- Application Information
AI Technical Summary
Problems solved by technology
Method used
Image
Examples
specific Embodiment 1
[0025] Glue the upper and lower sides of the core board 1 and paste the eucalyptus middle layer board 2. Under normal temperature, press 10 MPa, cold press for 30 minutes, trim the surface after cold pressing, and get a semi-finished product. The resulting semi-finished product was placed at a temperature of 110° C. under a pressure of 10 MPa, and hot-pressed for 8 minutes. After hot-pressing, the first health preservation was carried out for 7 days.
[0026] After the curing, the surface of the semi-finished product is sanded for the first time, and then the surface of the semi-finished product is greasy after sanding, and the steps of curing and sanding are repeated again.
[0027] The semi-finished product after the second sanding is polished, and the polished semi-finished product is glued on both sides and pasted with poplar board cortex 3. At normal temperature, the pressure is 10Mpa and cold pressed for 15 minutes.
[0028] After the cold pressing is finished, put the s...
specific Embodiment 2
[0030] Glue the upper and lower sides of the core board 1 and stick the eucalyptus wood middle layer board 2. Under normal temperature, the pressure is 9Mpa, and the cold pressing is carried out for 45 minutes. After the cold pressing, the surface is trimmed to obtain a semi-finished product. The resulting semi-finished product was placed at a temperature of 115° C. under a pressure of 9 MPa and hot-pressed for 8 minutes. After hot-pressing, the first health preservation was carried out for 7 days.
[0031] After the curing, the surface of the semi-finished product is sanded for the first time, and then the surface of the semi-finished product is greasy after sanding, and the steps of curing and sanding are repeated again.
[0032] The semi-finished product after the second sanding is polished, and the polished semi-finished product is glued on both sides and pasted with poplar board cortex 3. At normal temperature, the pressure is 9Mpa and cold pressed for 20 minutes.
[0033...
specific Embodiment 3
[0035] Glue the upper and lower sides of the core board 1 and paste the eucalyptus middle layer board 2. Under normal temperature, press 8 MPa, cold press for 30 minutes, trim the surface after cold pressing, and get a semi-finished product. The resulting semi-finished product was placed at a temperature of 120° C., pressure 8 MPa, and hot-pressed for 8 minutes. After hot-pressing, the first health preservation was carried out for 7 days.
[0036] After the curing, the surface of the semi-finished product is sanded for the first time, and then the surface of the semi-finished product is greasy after sanding, and the steps of curing and sanding are repeated again.
[0037] The semi-finished product after the second sanding is polished, and the polished semi-finished product is glued on both sides and pasted with poplar board cortex 3. At normal temperature, the pressure is 8Mpa and cold pressed for 30 minutes.
[0038] After the cold pressing is finished, put the semi-finished ...
PUM
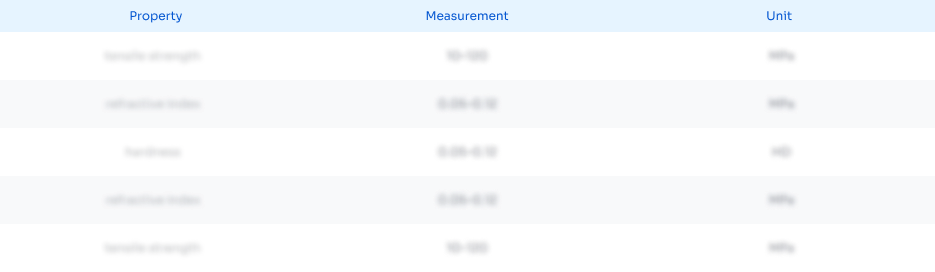
Abstract
Description
Claims
Application Information

- R&D
- Intellectual Property
- Life Sciences
- Materials
- Tech Scout
- Unparalleled Data Quality
- Higher Quality Content
- 60% Fewer Hallucinations
Browse by: Latest US Patents, China's latest patents, Technical Efficacy Thesaurus, Application Domain, Technology Topic, Popular Technical Reports.
© 2025 PatSnap. All rights reserved.Legal|Privacy policy|Modern Slavery Act Transparency Statement|Sitemap|About US| Contact US: help@patsnap.com