Method for testing braking force of muzzle brake
A technology of muzzle brake and muzzle, which is applied in the field of muzzle brake braking force testing, can solve the problems of reducing the structural strength reserve of the artillery, reducing the key performance of the artillery, and the large vibration response of the muzzle, so as to improve the development level, The effect of saving test costs and improving shooting intensity
- Summary
- Abstract
- Description
- Claims
- Application Information
AI Technical Summary
Problems solved by technology
Method used
Image
Examples
Embodiment Construction
[0025] The invention adopts the principle of strain measurement to realize the experimental test of the braking force of the muzzle brake. Select four measuring points symmetrically on a certain cross-section of the outer surface of the barrel 1 near the muzzle brake, paste a piece of one-way strain gauge 2 on each measuring point, and the direction of the sensitive grid is along the axial direction of the barrel 1. The upper and lower surface measuring point strain gauges 2 form an electric bridge system, while the left and right surface measuring point strain gauges 2 form another electric bridge system, and the strains obtained by the two electric bridge systems are averaged. When the artillery fires, in the post-effect period, the gas flow of the artillery impacts the muzzle brake, which applies a forward pulling force to the barrel 1, causing the barrel 1 to stretch and deform. The strain gauge 2 senses the tensile deformation, and the dynamic strain gauge transmits the e...
PUM
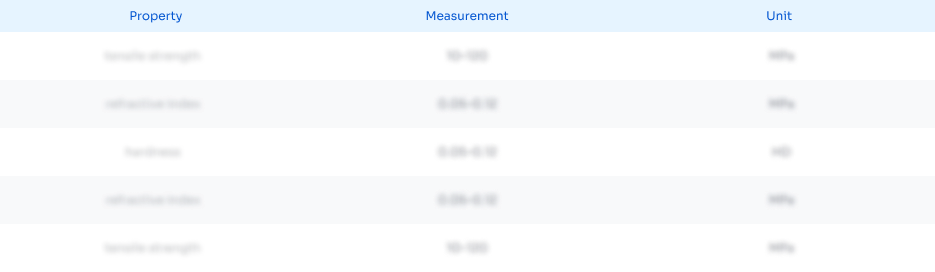
Abstract
Description
Claims
Application Information

- R&D Engineer
- R&D Manager
- IP Professional
- Industry Leading Data Capabilities
- Powerful AI technology
- Patent DNA Extraction
Browse by: Latest US Patents, China's latest patents, Technical Efficacy Thesaurus, Application Domain, Technology Topic, Popular Technical Reports.
© 2024 PatSnap. All rights reserved.Legal|Privacy policy|Modern Slavery Act Transparency Statement|Sitemap|About US| Contact US: help@patsnap.com