Intellectualized design method facing machine tool strut member ribbed slab layout with high specific stiffness
A design method and support technology, applied in computing, special data processing applications, instruments, etc., can solve problems such as low design efficiency, inability to realize intelligence and automation, and inability to obtain high specific stiffness design solutions, so as to achieve performance improvement, The effect of meeting the design requirements of high rigidity ratio
- Summary
- Abstract
- Description
- Claims
- Application Information
AI Technical Summary
Problems solved by technology
Method used
Image
Examples
Embodiment Construction
[0034] The present invention will be further described below in conjunction with accompanying drawings and examples.
[0035] According to the present invention, the intelligent design method for the rib plate layout of the machine tool supports with high specific stiffness is as follows: figure 1 As shown, it includes the following design stages and specific steps:
[0036] 1. Design stage 1: Construction of pseudo-3D generative space model
[0037] Firstly, the original solid structure of the machine tool support is simplified as a combination of internal ribs and peripheral panels. Next, the above-mentioned simplified combination is further abstracted into a pseudo-three-dimensional space model, which is composed of shell elements simulating the outer wall panels of the support and Matrix27 elements simulating the internal ribs of the support. According to the load-bearing relationship of the support, a peripheral wall plate is selected as the load-bearing surface, and a ...
PUM
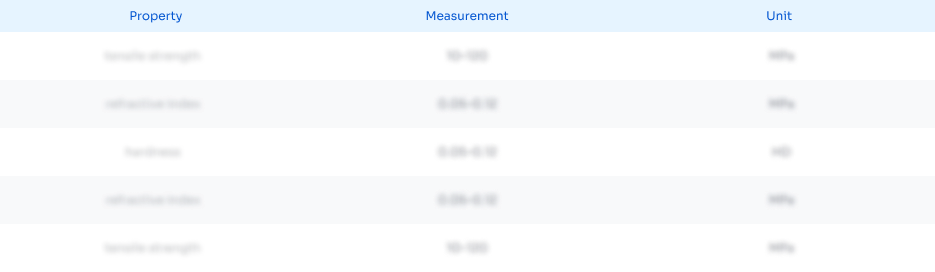
Abstract
Description
Claims
Application Information

- R&D
- Intellectual Property
- Life Sciences
- Materials
- Tech Scout
- Unparalleled Data Quality
- Higher Quality Content
- 60% Fewer Hallucinations
Browse by: Latest US Patents, China's latest patents, Technical Efficacy Thesaurus, Application Domain, Technology Topic, Popular Technical Reports.
© 2025 PatSnap. All rights reserved.Legal|Privacy policy|Modern Slavery Act Transparency Statement|Sitemap|About US| Contact US: help@patsnap.com