Manufacturing technique of imitation silk bleached cloth
A production process, silk imitation technology, applied in the field of dyeing and finishing technology, can solve the problem of not giving polyester fiber fabrics softness, drape, moisture absorption, breathability, antistatic, can not imitate silk fabrics to achieve natural texture, fabric whiteness is not easy to control and other problems, to achieve the effect of good whiteness consistency, avoid cylinder difference, and large added value
- Summary
- Abstract
- Description
- Claims
- Application Information
AI Technical Summary
Problems solved by technology
Method used
Examples
Embodiment 1
[0008] A production process for imitating silk bleached cloth, including the following steps: presetting, alkali weight reduction, dehydration, drying, setting and whitening, and calendering; since polyester is stretched during the spinning and forming process, the Residual stress, if the alkali reduction is carried out directly, it will cause shrinkage and fabric wrinkles. Therefore, pre-setting the gray fabric under a certain tension, setting the setting temperature to 185°C, and setting time to 35 seconds, which is conducive to smooth surface and stable size; The pre-shaped gray cloth has a slurry and a certain amount of oil remaining on the cloth surface. In the alkali reduction process, the polyester surface is etched with concentrated alkali to form pits on the surface, which eliminates the aurora of polyester filaments and increases the interweaving points of polyester. The gap makes the fabric feel soft, and at the same time, the cloth size and oil agent will swell and ...
Embodiment 2
[0010] The gray cloth is pre-shaped under a certain tension, the setting temperature is set at 190°C, and the setting time is 30 seconds, which is conducive to the flatness of the cloth surface and the stability of the size; the pre-shaped gray cloth has a slurry and a certain amount of oil on the cloth surface , in the alkali reduction process, caustic soda causes polyester to undergo alkali reduction, forming pits on the surface, eliminating the aurora of polyester filaments, making the fabric feel soft, and at the same time, the size and oil on the fibers swell and fall off, and the amount of alkali added 10g / l, set the alkali reduction temperature to 105°C, set the alkali reduction time to 50 minutes, add oligomer remover 2g / l, scouring agent 2g / l, bath softener 1g / l, bath The ratio is 1:6, after the alkali reduction is completed, the temperature is lowered to 70°C and the liquid is drained; the temperature of the incoming water is raised to 90°C for washing to remove the i...
PUM
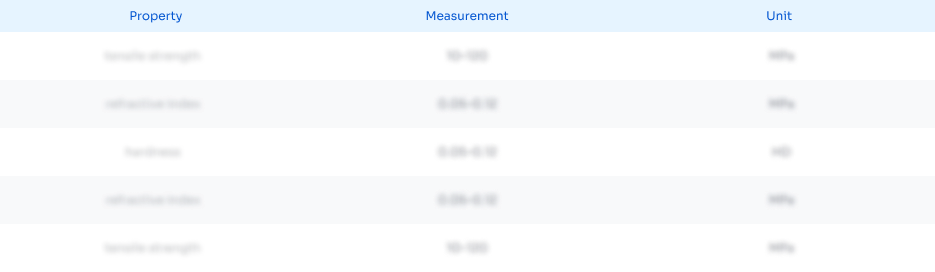
Abstract
Description
Claims
Application Information

- R&D Engineer
- R&D Manager
- IP Professional
- Industry Leading Data Capabilities
- Powerful AI technology
- Patent DNA Extraction
Browse by: Latest US Patents, China's latest patents, Technical Efficacy Thesaurus, Application Domain, Technology Topic, Popular Technical Reports.
© 2024 PatSnap. All rights reserved.Legal|Privacy policy|Modern Slavery Act Transparency Statement|Sitemap|About US| Contact US: help@patsnap.com