Polyether-b-polyamide (PEBA)/polyethyleneglycol (PEG) or polyoxyethylene (PEO) blend membrane, and preparation and application thereof
A technology of blending membranes and membrane materials, applied in membrane technology, semi-permeable membrane separation, chemical instruments and methods, etc., to achieve high separation performance and improve the effect of selectivity decline
- Summary
- Abstract
- Description
- Claims
- Application Information
AI Technical Summary
Problems solved by technology
Method used
Image
Examples
Embodiment 1
[0055] Add 5 grams of vacuum-dried Pebax1074 (m(PEO):m(PA12)=45:55, mass ratio) to 95 grams of n-butanol solvent, and stir at 80°C for 6 hours to form a uniform and transparent polymer After the solution, add 0.55 g of PEG200 to the polymer solution, continue to stir for 2 hours, and after forming a uniform and transparent solution again, perform negative pressure degassing; pour the defoamed casting solution into a clean horizontal glass plate In the smooth iron ring, the casting solution is evenly spread on the glass plate, and the temperature of the glass plate is kept at 50°C, and the solvent is volatilized, and the primary film is finally formed. The nascent film was carefully removed from the glass plate, placed in a vacuum oven, dried at 50° C. for 48 h, and the residual solvent was removed to obtain a PEBA / PEG200 (10%) blended homogeneous film with a PEG200 content of 10 wt.%, and Test its permeability (35°C).
[0056] The experimental result of table 1 embodiment 1 ...
Embodiment 2
[0059] Add 5 grams of vacuum-dried Pebax1074 to 95 grams of n-butanol solvent, stir at 80°C for 6 hours to form a uniform and transparent polymer solution, add 0.55 grams of PEG400 to the polymer solution, and continue stirring for 2 hours. After forming a uniform and transparent solution again, perform ultrasonic degassing, pour the defoamed casting solution into a smooth iron ring on a clean horizontal glass plate, so that the casting solution spreads evenly on the glass plate, and the temperature of the glass plate Keep at 50°C to volatilize the solvent and finally form a primary film. The nascent film was carefully removed from the glass plate, placed in a vacuum oven, dried at 50° C. for 48 h, and the residual solvent was removed to obtain a PEBA / PEG400 (10%) blended homogeneous film with a PEG400 content of 10 wt.%, and Test its permeability (35°C).
[0060] The experimental result of table 2 embodiment 2
[0061]
Embodiment 3
[0063] Add 5 grams of vacuum-dried Pebax1074 to 95 grams of n-butanol solvent, stir at 80°C for 6 hours to form a uniform and transparent polymer solution, add 0.55 grams of PEG600 to the polymer solution, and continue stirring for 2 hours. After forming a uniform and transparent solution again, let it stand for defoaming, and pour the defoamed casting solution into a smooth iron ring on a clean horizontal glass plate to spread the casting solution evenly on the glass plate. The temperature is kept at 50° C., and the solvent is volatilized to finally form a primary film. The nascent film was carefully removed from the glass plate, put into a vacuum oven, dried at 50°C for 48h, and the residual solvent was removed to obtain a PEBA / PEG600 (10%) blended homogeneous film with a PEG600 content of 10wt.%, and Test its permeability (35°C).
[0064] The experimental result of table 3 embodiment 3
[0065]
PUM
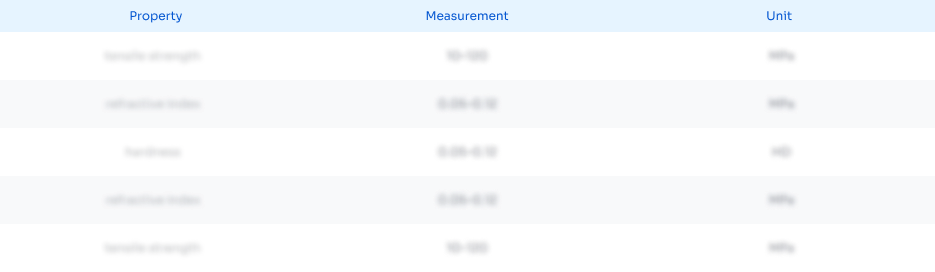
Abstract
Description
Claims
Application Information

- R&D
- Intellectual Property
- Life Sciences
- Materials
- Tech Scout
- Unparalleled Data Quality
- Higher Quality Content
- 60% Fewer Hallucinations
Browse by: Latest US Patents, China's latest patents, Technical Efficacy Thesaurus, Application Domain, Technology Topic, Popular Technical Reports.
© 2025 PatSnap. All rights reserved.Legal|Privacy policy|Modern Slavery Act Transparency Statement|Sitemap|About US| Contact US: help@patsnap.com