Preparation method of permanent magnet material with linear remanence temperature coefficient
A technology of temperature coefficient and permanent magnet materials, applied in the direction of magnetic materials, magnetic objects, electrical components, etc., can solve the technical design and production difficulties of high-precision devices, and achieve the effect of low temperature coefficient
- Summary
- Abstract
- Description
- Claims
- Application Information
AI Technical Summary
Problems solved by technology
Method used
Image
Examples
Embodiment 1
[0017] According to the preparation method of the linear remanence temperature coefficient permanent magnet material proposed by the present invention, the alloys A and B are respectively smelted in a vacuum induction furnace, and the composition is shown in Table 1. First at N 2 Under protection, the two alloys were crushed to powders on the order of millimeters, and then the crushed alloys A and B were mixed in a ratio of 50:50, and rolling ball milling was carried out under the protection of absolute alcohol for 5 hours. The particle size of the mixed powder after ball milling was Reaching the micron level, after the above-mentioned powder is formed, it is sintered at 1230°C for 1 hour, then cooled to 1180°C at a rate of 1.5°C / min for 3 hours of solid solution treatment, then quenched and placed in the Room temperature, obtain preliminary blank; After preliminary blank is kept at 760 DEG C for 20 hours, cool to 600 DEG C with 1.5 DEG C / min speed and keep warm for 3.5 hours,...
Embodiment 2
[0022] Alloys A and B were smelted in a vacuum induction furnace, and their compositions are shown in Table 2. First, under the protection of Ar, the two alloys were crushed to millimeter-scale powders, and then the crushed alloys A and B were mixed in a ratio of 40:60, and rolling ball milling was carried out under the protection of absolute alcohol for 10 hours. The particle size of the powder reaches the micron level. After the above powder is formed, it is sintered at 1255°C for 0.5 hours, then cooled to 1220°C at a speed of 1.5°C / min for 2 hours of solid solution treatment, and quenched to Room temperature, obtain preliminary blank; After preliminary blank is incubated at 830 DEG C for 10 hours, be cooled to 600 DEG C with 1.5 DEG C / min speed and be incubated 2 hours, then with 2.0 DEG C / min speed cooling 500 DEG C and be incubated 4 hours, Then cool to 400°C at a rate of 2.2°C / min and keep it warm for 10 hours, and quench it to room temperature to obtain a permanent magn...
Embodiment 3
[0026] Alloys A and B were smelted in a vacuum induction furnace, and their compositions are shown in Table 3. First, under the protection of N2, the two alloys were crushed to powders of the order of millimeters, and then the crushed alloys A and B were mixed at a ratio of 55:45, and rolling ball milling was carried out under the protection of gasoline for 8 hours. The particle size of the mixed powder after ball milling Reaching the micron level, after the above powder is formed, it is sintered at 1240°C for 0.5 hours, then cooled to 1200°C at a rate of 1.5°C / min for 3 hours of solid solution treatment, and quenched to room temperature. Obtain the preliminary blank; After the preliminary blank is kept at 800°C for 15 hours, it is cooled to 600°C and kept at 1.5°C / min for 3 hours, then cooled at 2.0°C / min for 500°C and kept at 3 hours for 3 hours. Cool at 2.2°C / min to 400°C and hold for 15 hours, then quench and let it cool to room temperature to obtain a permanent magnetic m...
PUM
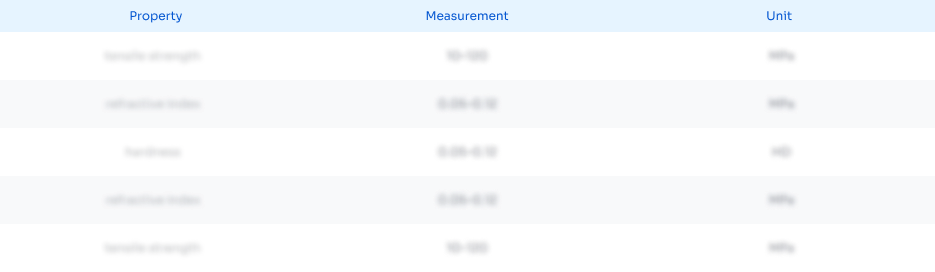
Abstract
Description
Claims
Application Information

- R&D Engineer
- R&D Manager
- IP Professional
- Industry Leading Data Capabilities
- Powerful AI technology
- Patent DNA Extraction
Browse by: Latest US Patents, China's latest patents, Technical Efficacy Thesaurus, Application Domain, Technology Topic, Popular Technical Reports.
© 2024 PatSnap. All rights reserved.Legal|Privacy policy|Modern Slavery Act Transparency Statement|Sitemap|About US| Contact US: help@patsnap.com