Double mobile crane cooperative hoisting simulation method based on kinematics and dynamics
A technology of mobile cranes and simulation methods, applied in the direction of instruments, simulators, control/regulation systems, etc., can solve problems such as poor practicability, complex models, and many physical parameters, and achieve the effect of improving efficiency and simplifying the modeling process
- Summary
- Abstract
- Description
- Claims
- Application Information
AI Technical Summary
Problems solved by technology
Method used
Image
Examples
Embodiment 1
[0024] PhysX is a computing engine that can make the movement of virtual objects conform to the real laws of physics. It can calculate a large amount of data in physical simulations by the GPU of the computer. PhysX provides the abstraction of rigid bodies in reality, which are called actors in the engine, and are divided into two types of rigid bodies: kinematic roles and dynamic roles; at the same time, it also provides various dynamic constraints in reality, which are called hinges in the engine ( Joint), including distance hinges, rotary hinges, translational hinges, spherical hinges, universal hinges, etc. Therefore, the above two-machine simulation model can be easily realized by using PhysX.
[0025] In the process of modeling, the main crane and auxiliary crane are modeled by kinematics. The crane is composed of kinematic rigid body of dismounting, boarding, jib and lifting pulley block. The relative motion of dismounting and ground is modeled as a moving The relative...
PUM
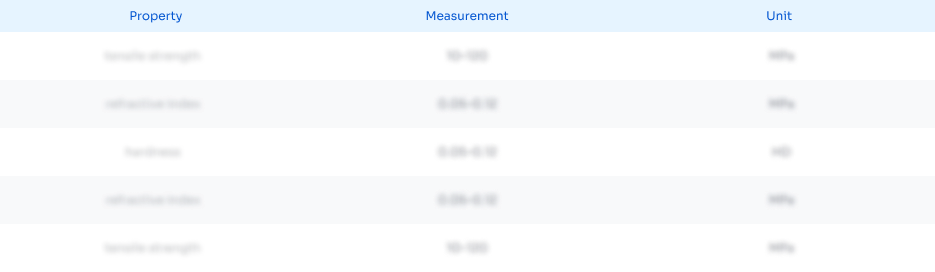
Abstract
Description
Claims
Application Information

- R&D
- Intellectual Property
- Life Sciences
- Materials
- Tech Scout
- Unparalleled Data Quality
- Higher Quality Content
- 60% Fewer Hallucinations
Browse by: Latest US Patents, China's latest patents, Technical Efficacy Thesaurus, Application Domain, Technology Topic, Popular Technical Reports.
© 2025 PatSnap. All rights reserved.Legal|Privacy policy|Modern Slavery Act Transparency Statement|Sitemap|About US| Contact US: help@patsnap.com