Environment-friendly type crust leather production method
A production method and an environment-friendly technology, applied in the field of leather manufacturing, can solve the problems of a large number of chrome-containing leather wastes, pollute the environment, cannot be effectively treated, etc., to improve the shrinkage temperature and comprehensive performance, protect the environment, and improve the content of chrome-containing wastewater. reduced effect
- Summary
- Abstract
- Description
- Claims
- Application Information
AI Technical Summary
Problems solved by technology
Method used
Examples
Embodiment 1
[0031] (1) No pickling tanning
[0032] Put the limed yellow cowhide in the drum for deliming, softening, washing and water control. Then add 50% normal temperature water of gray leather quality in the rotating drum, then add gray leather quality 3% non-pickling chrome-free tanning agent TWS, 3% non-pickling chrome-free tanning agent TWT, and rotate for 4 hours. Then add baking soda with 1.0% gray leather mass in the drum, adjust the pH value to 7.8-8.0, and then rotate for 1 hour. Finally, add hot water with 150% gray skin mass into the drum, keep the temperature in the drum at 38-40°C, rotate for 3 hours, stop the drum overnight, and rise the drum the next day to obtain wet white skin with a shrinkage temperature of 87°C.
[0033] (2) Retanning filling
[0034] Squeeze, smooth, and rewet the wet white hide of yellow cattle that has not been pickled and tanned to obtain a smooth peel. Put the shaved hides into the drum, add hot water with 50% weight of the shaved hides, ke...
Embodiment 2
[0041] (1) No pickling tanning
[0042] Put the limed yellow cowhide in the drum for deliming, softening, washing and water control. Then add normal temperature water with 100% gray hide quality in the rotating drum, then add 5% gray hide quality without pickling and chrome-free tanning agent TWS, and rotate for 6 hours. Then add baking soda with 1.2% gray leather mass in the drum, adjust the pH value to 8.0-8.2, and then rotate for 1.5 hours. Finally, add hot water with 250% gray skin mass into the drum, keep the temperature in the drum at 38-40°C, rotate for 4 hours, stop the drum overnight, and rise the drum the next day to obtain wet white skin with a shrinkage temperature of 85°C.
[0043] (2) Retanning filling
[0044] Squeeze, smooth, and rewet the wet white hide of yellow cattle that has not been pickled and tanned to obtain a smooth peel. Put the shaved hide into the drum, add hot water with 100% shaved hide weight, keep the temperature inside the drum at 45°C, add...
Embodiment 3
[0051] (1) No pickling tanning
[0052] Put the limed sheepskin in the drum for deliming, softening, washing and water control. Then add 80% normal temperature water of gray leather quality in the rotating drum, then add 9% gray leather quality without pickling and chrome-free tanning agent TWT, and rotate for 2 hours. Then add 0.2% baking soda of gray skin mass to the drum, adjust the pH value to 7.2-7.5, and then rotate for 0.5 hour. Finally, add hot water with 200% gray skin mass into the drum, keep the temperature in the drum at 38-40°C, rotate for 2 hours, stop the drum overnight, and rise the drum the next day to obtain wet white skin with a shrinkage temperature of 89°C.
[0053] (2) Retanning filling
[0054] Squeeze, smooth, and rewet the wet white sheep hide that has not been pickled and tanned to obtain a smooth peel. Put the shaved hide into the drum, add hot water with 50% weight of the shaved hide, keep the temperature inside the drum at 40°C, add acrylic reta...
PUM
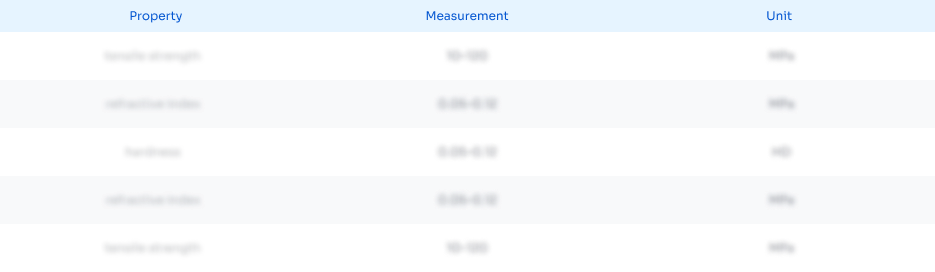
Abstract
Description
Claims
Application Information

- R&D
- Intellectual Property
- Life Sciences
- Materials
- Tech Scout
- Unparalleled Data Quality
- Higher Quality Content
- 60% Fewer Hallucinations
Browse by: Latest US Patents, China's latest patents, Technical Efficacy Thesaurus, Application Domain, Technology Topic, Popular Technical Reports.
© 2025 PatSnap. All rights reserved.Legal|Privacy policy|Modern Slavery Act Transparency Statement|Sitemap|About US| Contact US: help@patsnap.com