Foaming agent for forming CO2 foams and preparation method thereof
A foaming agent and foaming technology, applied in the chemical field, can solve the problems of not being able to use large doses, harsh use conditions, and low foaming volume, etc.
- Summary
- Abstract
- Description
- Claims
- Application Information
AI Technical Summary
Problems solved by technology
Method used
Image
Examples
Embodiment 1
[0025] This example is used for the preparation and performance evaluation of foaming agent
[0026] Accurately weigh 100 parts by weight of alkyl hydroxypropyl phosphate betaine (n=14), 5 parts by weight of alkyl phosphate (n=4, m=8), fatty alcohol polyoxyethylene ether sodium sulfate (n= 12, m=3) 8 parts by weight, 7 parts by weight lauryl imidazoline betaine, dissolved in 120 parts by weight simulated brine (NaCl 1%, CaCl 2 0.02%), use a glass rod to slowly stir and dissolve to avoid foam formation, that is, a foaming agent system is obtained. Use simulated brine (NaCl 1%, CaCl 2 0.02%) was formulated into a foaming liquid of 3000mg / L and 5000mg / L. The foaming volume was 620mL and 640mL, and the half-life was 20min and 22min, respectively, measured by the Roche foam meter at 80℃.
Embodiment 2
[0028] This example is used for the preparation and performance evaluation of foaming agent
[0029] Accurately weigh 100 parts by weight of alkyl hydroxypropyl phosphate betaine (n=14), 3.5 parts by weight of alkyl phosphate (n=4, m=8), fatty alcohol polyoxyethylene ether sodium sulfate (n= 12, m=3) 1 part by weight, 8 parts by weight lauryl imidazoline betaine, dissolved in 60 parts by weight simulated brine (NaCl 1%, CaCl 2 0.02%), use a glass rod to slowly stir and dissolve to avoid foam formation, that is, a foaming agent system is obtained. Use simulated brine (NaCl 1%, CaCl 2 0.02%) formulated into 2000mg / L, 3000mg / L foaming liquid. The foaming volume was 640mL and 650mL, and the half-life was 19min and 24min, respectively, measured by the Roche foam meter at 80℃.
Embodiment 3
[0031] This example is used for the preparation and performance evaluation of foaming agent
[0032] Accurately weigh 100 parts by weight of alkyl hydroxypropyl phosphate betaine (n=14), 10 parts by weight of alkyl phosphate (n=4, m=8), fatty alcohol polyoxyethylene ether sodium sulfate (n= 12, m=3) 1 part by weight, 4 parts by weight lauryl imidazoline betaine, dissolved in 90 parts by weight simulated brine (NaCl 1%, CaCl 2 0.02%), slowly added to the beaker, slowly stirred with a glass rod to dissolve, to avoid the formation of foam, that is, a foaming agent system. Use simulated brine (NaCl 1%, CaCl 2 0.02%) was formulated into 2000mg / L, 5000mg / L foaming liquid. The foaming volume measured by Roche foam meter at 80°C was 600 mL and 620 mL, and the half-life was 28 min and 23 min respectively.
PUM
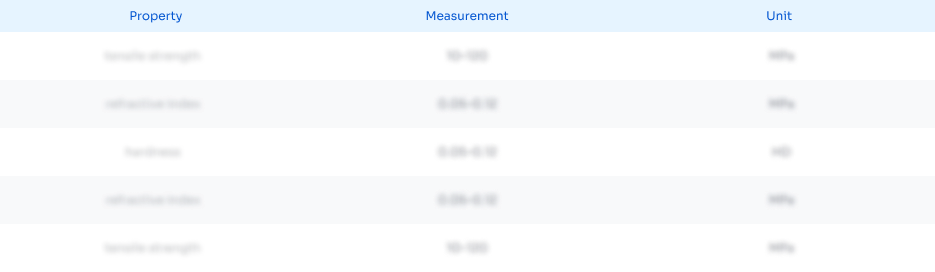
Abstract
Description
Claims
Application Information

- R&D
- Intellectual Property
- Life Sciences
- Materials
- Tech Scout
- Unparalleled Data Quality
- Higher Quality Content
- 60% Fewer Hallucinations
Browse by: Latest US Patents, China's latest patents, Technical Efficacy Thesaurus, Application Domain, Technology Topic, Popular Technical Reports.
© 2025 PatSnap. All rights reserved.Legal|Privacy policy|Modern Slavery Act Transparency Statement|Sitemap|About US| Contact US: help@patsnap.com