Rotary-motion-oriented reed type linear micro-driving mechanism
A rotary motion, reed-type technology, applied in installation, optics, instruments, etc., can solve the problem that the best matching angle of the crystal is not easy to adjust, and achieve the advantages of convenient debugging and maintenance, simple structure, high reliability and stability Effect
- Summary
- Abstract
- Description
- Claims
- Application Information
AI Technical Summary
Problems solved by technology
Method used
Image
Examples
specific Embodiment approach 1
[0010] Specific implementation mode one: combine Figure 1 to Figure 3 Describe this embodiment, a reed type linear micro-drive mechanism for rotary motion in this embodiment includes a stepper motor 1, a reducer 2, a rigid coupling 3, a rolling screw 4, a bearing seat 5, and a rolling bearing assembly 6 , rolling nut 7, connecting block 9, base 10, nut seat plate 11, base bending plate 12, rolling guide rail 8, slider 17, four reed pressure plates 13, two upper splints 14, two lower splints 15 , two reeds 16;
[0011] The output shaft of the stepping motor 1 is connected to the reducer 2, and the side wall on the output side of the reducer 2 is installed with a base bending plate 12, and the output shaft of the reducer 2 passes through the base bending plate 12 and passes through the rigid coupling The device 3 is connected with one end of the rolling screw 4, the base 10 is installed on the base curved plate 12, the rolling guide rail 8 and the bearing housing 5 are install...
specific Embodiment approach 2
[0012] Specific implementation mode two: combination figure 1 The present embodiment will be described. The speed reducer 2 of the present embodiment is a planetary speed reducer. Other compositions and connections are the same as in the first embodiment.
[0013] The linear micro-drive mechanism can convert linear motion into rotary motion through the connection with the connecting block, the adjustment range of the rotary motion is ±15mrad, and the adjustment accuracy is better than 5urad. The micro-drive mechanism is mainly used to drive the rotary motions such as pitch and yaw of the optical lens.
PUM
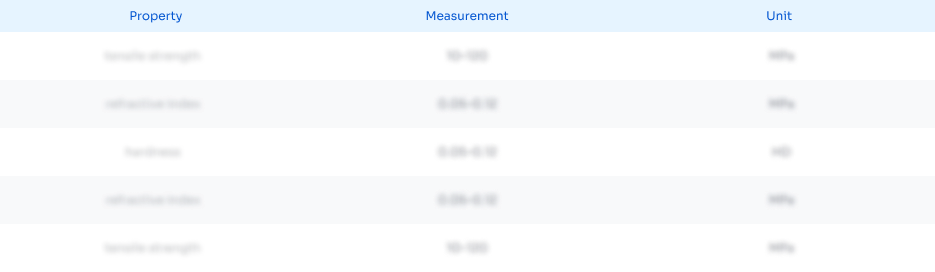
Abstract
Description
Claims
Application Information

- R&D
- Intellectual Property
- Life Sciences
- Materials
- Tech Scout
- Unparalleled Data Quality
- Higher Quality Content
- 60% Fewer Hallucinations
Browse by: Latest US Patents, China's latest patents, Technical Efficacy Thesaurus, Application Domain, Technology Topic, Popular Technical Reports.
© 2025 PatSnap. All rights reserved.Legal|Privacy policy|Modern Slavery Act Transparency Statement|Sitemap|About US| Contact US: help@patsnap.com