Fuzzing roller rolled by carbon fiber composite material in two-step method
A composite material and carbon fiber technology, used in textiles and papermaking, roughening, fabric surface trimming, etc., can solve the problems of poor fatigue resistance of steel raising rollers, heavy raising rollers, serious energy loss, etc., to save equipment. The effect of maintenance cost, equipment energy consumption reduction and life extension
- Summary
- Abstract
- Description
- Claims
- Application Information
AI Technical Summary
Problems solved by technology
Method used
Image
Examples
Embodiment Construction
[0012] A two-step carbon fiber composite material rolling raising roller comprises a roller body of the raising roller and shaft heads arranged at both ends of the roller body.
[0013] (1) First of all, carry out the first lay-up design, first wind the carbon fiber prepreg on the designed mold mandrel, after reaching the required thickness of the lay-up, then put it into the curing box for curing, and demould after cooling. Into a carbon fiber liner for spare.
[0014] (2) The shaft head includes the front part of the shaft head and the bonding section plugged into the carbon fiber liner, a reinforced shoulder is arranged between the front part of the shaft head and the bonding section, and the outer surface of the bonding section Grooves for easy bonding are processed, and the bonding section is coated with adhesive and then inserted into the carbon fiber inner tube for bonding, and the reinforced shoulder is blocked at the end of the carbon fiber inner tube. The groove on ...
PUM
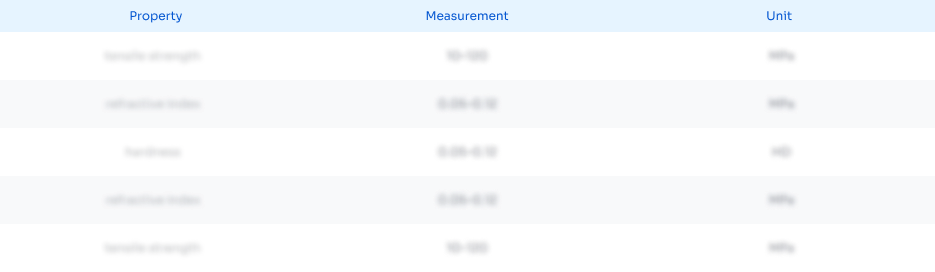
Abstract
Description
Claims
Application Information

- R&D Engineer
- R&D Manager
- IP Professional
- Industry Leading Data Capabilities
- Powerful AI technology
- Patent DNA Extraction
Browse by: Latest US Patents, China's latest patents, Technical Efficacy Thesaurus, Application Domain, Technology Topic, Popular Technical Reports.
© 2024 PatSnap. All rights reserved.Legal|Privacy policy|Modern Slavery Act Transparency Statement|Sitemap|About US| Contact US: help@patsnap.com