1050-H16 aluminum alloy plate strip and production method thereof
An aluminum alloy strip and production method technology, applied in the field of aluminum alloy manufacturing, can solve problems such as high requirements for annealing temperature uniformity, high temperature control requirements for annealing furnaces, unsatisfactory surface quality, etc., and achieves elimination of uneven structure of ingots. , The mechanical properties are stable and qualified, and the effect of reducing the instability of yield strength
- Summary
- Abstract
- Description
- Claims
- Application Information
AI Technical Summary
Problems solved by technology
Method used
Image
Examples
Embodiment 1
[0023] The production process of the 1050-H16 aluminum alloy plate and strip described in this embodiment includes: melting and casting→sawing→face milling→heating→hot rolling→cold rolling. The specific process parameters are as follows:
[0024] (1) Melting and casting: the mass percentage of the chemical composition of the ingot after melting and casting is controlled at Si: 0.03%, Fe: 0.28%, Cu≤0.05%, Mn≤0.05%, Mg≤0.05%, Zn ≤0.05%, Ti: 0.015%, other impurities individually ≤0.02%, total ≤0.10%, the rest is Al; the melting temperature is 730-750°C, the refining temperature is 740°C, the casting temperature is 670°C, and the casting speed is 65mm / min;
[0025] (2) Face milling: use a milling machine to mill the large and small faces of the ingot respectively, and the milling amounts are 8mm and 7mm respectively;
[0026] (3) Heating: the ingot heating temperature is 560-570°C, the holding time is 3 hours, and the heat preservation time is 450-470°C for 3 hours to be released...
Embodiment 2
[0034] The production process of the 1050-H16 aluminum alloy plate and strip described in this embodiment includes: melting and casting→sawing→face milling→heating→hot rolling→cold rolling. The specific process parameters are as follows:
[0035] (1) Melting and casting: the alloy chemical composition (mass percentage) of the ingot is controlled at Si: 0.10%, Fe: 0.38%, Cu≤0.05%, Mn≤0.05%, Mg≤0.05%, Zn≤0.05%, Ti: 0.01 %, other impurities individually ≤0.02%, total ≤0.10%, and the rest are Al. The melting temperature is 730-750°C, the refining temperature is 750°C, the casting temperature is 700°C, and the casting speed is 55mm / min.
[0036] (2) Face milling: use a milling machine to mill the large face and the small face of the ingot respectively, and the milling amount is 8mm and 6mm respectively;
[0037] (3) Heating: the ingot heating temperature is 570°C, the holding time is 3 hours, and it is turned to 470°C for 3 hours and released from the furnace.
[0038] (4) Hot r...
Embodiment 3
[0044]The production process of the 1050-H16 aluminum alloy plate and strip described in this embodiment includes: melting and casting→sawing→face milling→heating→hot rolling→cold rolling. The specific process parameters are as follows:
[0045] (1) Melting and casting: the alloy chemical composition (mass fraction) of the ingot is controlled at Si: 0.05%, Fe: 0.20%, Cu≤0.05%, Mn≤0.05%, Mg≤0.05%, Zn≤0.05%, Ti: 0.01 %, other impurities individually ≤0.02%, total ≤0.10%, and the rest are Al. The melting temperature is 730-750°C, the refining temperature is 745°C, the casting temperature is 695°C, and the casting speed is 55mm / min.
[0046] (2) Face milling: use a milling machine to mill the large face and the small face of the ingot respectively, and the milling amount is 10mm and 8mm respectively;
[0047] (3) Heating: the ingot is heated at 550°C, held for 3 hours, turned to 500°C for 3 hours and released from the furnace.
[0048] (4) Hot rolling: After hot rough rolling a...
PUM
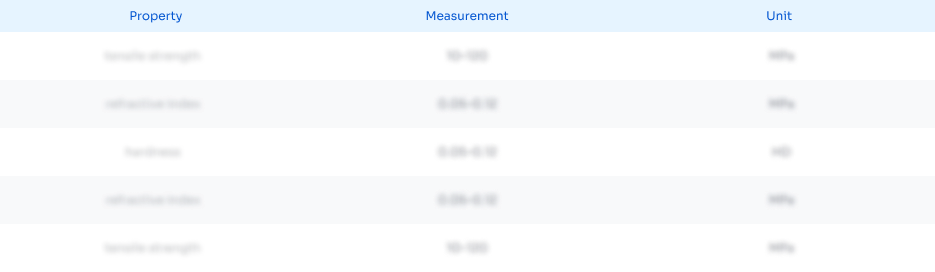
Abstract
Description
Claims
Application Information

- Generate Ideas
- Intellectual Property
- Life Sciences
- Materials
- Tech Scout
- Unparalleled Data Quality
- Higher Quality Content
- 60% Fewer Hallucinations
Browse by: Latest US Patents, China's latest patents, Technical Efficacy Thesaurus, Application Domain, Technology Topic, Popular Technical Reports.
© 2025 PatSnap. All rights reserved.Legal|Privacy policy|Modern Slavery Act Transparency Statement|Sitemap|About US| Contact US: help@patsnap.com