Durable cable body wound with spiral bar adhesive tapes and manufacturing method of cable body
A tendon tape and durability technology, applied in the field of anti-wind and rain-induced vibration cable body and its production, can solve the problems of cable repair failure, cable body sheath cracking, sheath light aging, etc., to achieve good wind and rain resistance Exciting vibration, improving service life, and good surface quality
- Summary
- Abstract
- Description
- Claims
- Application Information
AI Technical Summary
Problems solved by technology
Method used
Image
Examples
Embodiment 1
[0053] Embodiment 1: A durable cable body made of a single-layer PE cable body wound with a spiral rib tape.
[0054] Such as Figure 1-1~Figure 1-2 As shown, the durable cable body of the wound spiral rib tape includes a steel wire bundle 1, a winding tape 2 and a high-density polyethylene sheath 3, and after the steel wire bundle 1 is wrapped into a bundle by the winding tape 2, the high-density polyethylene Ethylene forms a high-density polyethylene sheath 3, and outside the high-density polyethylene sheath 3 one A spiral-rib adhesive tape 5 laminated by spiral winding; the surface of the spiral-rib adhesive tape 5 has two parallel ribs 501 .
Embodiment 2
[0055] Embodiment 2: a durable cable body with double-layer PE cable body wound with spiral rib tape.
[0056] Such as Figure 2-1~Figure 2-2 As shown, the durable cable body of the double-layer PE cable body wrapped with a spiral rib tape includes a steel wire bundle 1, a winding tape 2 and a high-density polyethylene sheath, and the steel wire bundle 1 is wrapped into a bundle by the winding tape 2 , heat-extruded high-density polyethylene to form an inner layer of high-density polyethylene sheath 3, and then heat-extruded high-density polyethylene to form an outer layer of high-density polyethylene sheath 4 outside the inner layer of high-density polyethylene sheath 3, There is a layer of spiral rib tape 5 attached by spiral winding outside the outer high-density polyethylene sheath 4; the surface of the spiral rib tape 5 has two raised parallel ribs 501.
[0057] In embodiment one and embodiment two, described spiral rib adhesive tape 5 can be single-layer spiral rib adhe...
Embodiment 3
[0062] Embodiment three: a method for manufacturing a durable cable body wound with a spiral rib tape, there are two methods for making the cable body:
[0063] The first method is: the durable cable body wrapped with spiral rib tape is completed in the cable body manufacturer. Density polyethylene sheath, and then a layer of lap-joint spiral rib tape is pasted on the outside of the high-density polyethylene sheath of the cable body by spiral winding. The lap-joint spiral rib tape includes a lap-joint single-layer spiral rib Adhesive tape 51a is either pasted or calendered a layer of protective film on the lap-joint single-layer spiral-rib adhesive tape 51a or a lap-joint composite spiral-rib adhesive tape 53a formed by spraying or brushing a layer of protective layer 52 .
[0064] The second method is: the durable cable body wrapped with spiral rib tape is completed at the construction site;
[0065] The specific method is: first wrap the steel wire bundles of the cable stay...
PUM
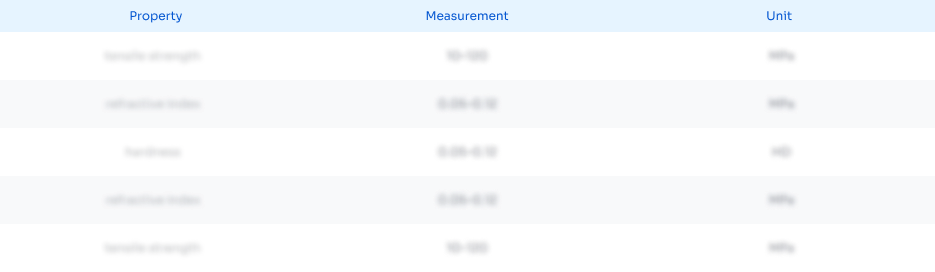
Abstract
Description
Claims
Application Information

- R&D
- Intellectual Property
- Life Sciences
- Materials
- Tech Scout
- Unparalleled Data Quality
- Higher Quality Content
- 60% Fewer Hallucinations
Browse by: Latest US Patents, China's latest patents, Technical Efficacy Thesaurus, Application Domain, Technology Topic, Popular Technical Reports.
© 2025 PatSnap. All rights reserved.Legal|Privacy policy|Modern Slavery Act Transparency Statement|Sitemap|About US| Contact US: help@patsnap.com