Wall board creep age forming method based on finite element mould profile rebound compensation
A technology of creep aging forming and mold surface, which is applied in special data processing applications, instruments, electrical digital data processing, etc. It can solve the problems of unfavorable parts accurate forming, failure to reflect the springback characteristics of parts, and labor and material resources consumption. Achieve the effects of prolonging the service life, reducing the number of process tests and mold repairs, and improving the forming accuracy
- Summary
- Abstract
- Description
- Claims
- Application Information
AI Technical Summary
Problems solved by technology
Method used
Image
Examples
Embodiment
[0058] Taking the shape of the target part as the initial mold surface for the first time, a finite element analysis model of a typical analog part is established, in which the mold is discretized by the rigid shell element R3D4; the size of the sheet is 751mm×761mm×3mm mm, and the large strain shell element S4R is used for discretization. discrete. The part material is aluminum alloy 7075T651, and the creep strain material model can be selected from the Norton-Baliley creep constitutive equation. The creep tensile test is carried out according to the metal creep tensile and durability test methods, and the least square method is used to fit the test data. Get A and m, n values, the basic parameters of the material are shown in the table below.
[0059]
[0060] Apply the mold surface optimization system, set the mold repair coefficient to c=1, and the maximum allowable gap tolerance to 0.5mm, and carry out the mold surface optimization calculation. After 4 finite element ...
PUM
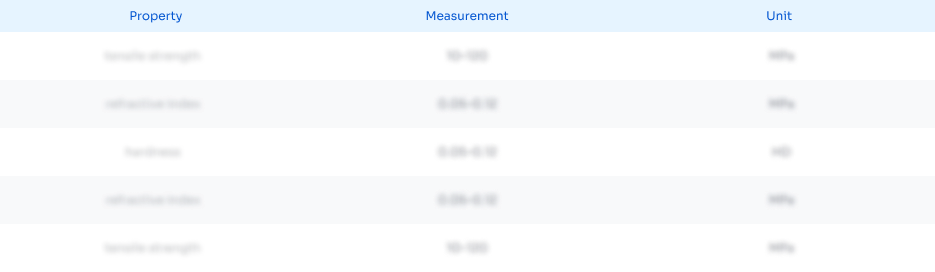
Abstract
Description
Claims
Application Information

- R&D
- Intellectual Property
- Life Sciences
- Materials
- Tech Scout
- Unparalleled Data Quality
- Higher Quality Content
- 60% Fewer Hallucinations
Browse by: Latest US Patents, China's latest patents, Technical Efficacy Thesaurus, Application Domain, Technology Topic, Popular Technical Reports.
© 2025 PatSnap. All rights reserved.Legal|Privacy policy|Modern Slavery Act Transparency Statement|Sitemap|About US| Contact US: help@patsnap.com