Twisted bar surface rust prevention method
A technology of threaded steel bar and surface temperature, which is applied in the direction of metal material coating process, coating, solid-state diffusion coating, etc., can solve the problems of fast rusting of steel bars, general anti-rust effect, and decline in the appearance quality of steel bars
- Summary
- Abstract
- Description
- Claims
- Application Information
AI Technical Summary
Problems solved by technology
Method used
Image
Examples
Embodiment Construction
[0009] In order to overcome the problems in the prior art, the invention provides a method for preventing rust on the surface of threaded steel bars. According to the antirust method for the surface of the threaded steel bar of the present invention, the surface of the threaded steel bar is treated with a steam bath to form a protective layer on the surface of the threaded steel bar, thereby obtaining a threaded steel bar with good surface gloss.
[0010] The principle adopted by the on-line antirust method for threaded steel bar of the present invention is that at high temperature, steam and iron undergo an oxidation-reduction reaction, so that the oxide scale generated on the surface of the threaded steel bar is formed of Fe 3 o 4 and Fe 2 o 3 Mainly, reduce the easily oxidizable substances produced by the decomposition of FeO, so that the easily oxidized and corroded substances in the air will be denatured at high temperature to form stable oxides, so as to achieve the pu...
PUM
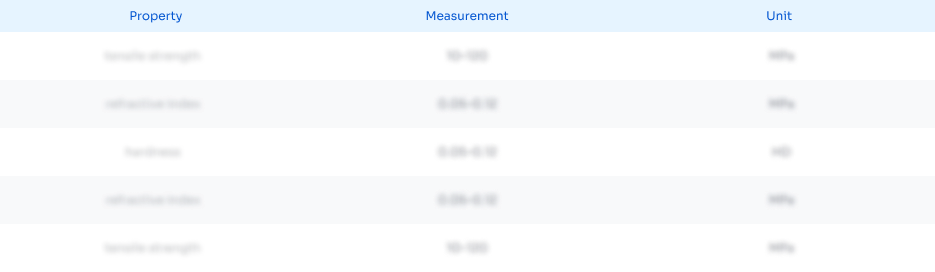
Abstract
Description
Claims
Application Information

- Generate Ideas
- Intellectual Property
- Life Sciences
- Materials
- Tech Scout
- Unparalleled Data Quality
- Higher Quality Content
- 60% Fewer Hallucinations
Browse by: Latest US Patents, China's latest patents, Technical Efficacy Thesaurus, Application Domain, Technology Topic, Popular Technical Reports.
© 2025 PatSnap. All rights reserved.Legal|Privacy policy|Modern Slavery Act Transparency Statement|Sitemap|About US| Contact US: help@patsnap.com