Novel technology for chloral industrial production
A technology for the industrial production of chloral, applied in organic chemistry, separation/purification of carbonyl compounds, etc., can solve the problems of incomplete treatment, high cost of energy consumption, high treatment cost, etc., and achieve the effect of improving the utilization rate of raw materials
- Summary
- Abstract
- Description
- Claims
- Application Information
AI Technical Summary
Problems solved by technology
Method used
Image
Examples
Embodiment 1
[0020] Chlorine oil (containing 65% aldehyde, 6% hydrogen chloride) enters the chlorine oil preheater at a flow rate of 1000kg / h, and enters the bottom of the continuous extraction tower after being preheated to 50°C; the chloroform flow rate is controlled at 1000kg / h and enters the chloroform preheater After being preheated to 50°C, it enters the continuous extraction tower; after the two phases are fully mass-transferred in the tower, the water phase (18% dilute hydrochloric acid) overflows from the top of the tower, and the oil phase is discharged from the bottom of the tower into the intermediate tank.
[0021] The oil phase in the intermediate tank is pumped to the light removal tower with corrugated ceramic packing. The temperature of the tower bottom is controlled at 108°C and the temperature at the top of the tower is 61°C. A very small amount of water (6kg / h) is separated as dilute hydrochloric acid into the dilute hydrochloric acid storage tank. The liquid in the bot...
Embodiment 2
[0023] Chlorine oil (containing 64% aldehyde, 5.5% hydrogen chloride) enters the chlorine oil preheater at a flow rate of 1000kg / h, and enters the bottom of the continuous extraction tower after being preheated to 20°C; controls the flow rate of chloroform at 2000kg / h and enters the chloroform preheater After being preheated to 20°C, it enters the continuous extraction tower; after the two phases are fully mass-transferred in the tower, the water phase (17% dilute hydrochloric acid) overflows from the top of the tower, and the oil phase is discharged from the bottom of the tower into the intermediate tank.
[0024] The oil phase in the intermediate tank is pumped to the light removal tower with corrugated ceramic packing. The temperature of the tower bottom is controlled at 108°C and the temperature at the top of the tower is 61°C. A very small amount of water (6kg / h) is separated as dilute hydrochloric acid into the dilute hydrochloric acid storage tank. The liquid in the bot...
Embodiment 3
[0026] Chlorine oil (containing 64% aldehyde, 5.5% hydrogen chloride) enters the chlorine oil preheater at a flow rate of 1000kg / h, and enters the bottom of the continuous extraction tower after being preheated to 80°C; controls the flow rate of chloroform to 500kg / h and enters the chloroform preheater After being preheated to 80°C, it enters the continuous extraction tower; after the two phases are fully mass-transferred in the tower, the water phase (19% dilute hydrochloric acid) overflows from the top of the tower, and the oil phase is discharged from the bottom of the tower into the intermediate tank.
[0027] The oil phase in the intermediate tank is pumped to the light removal tower with corrugated ceramic packing. The temperature of the tower bottom is controlled at 108°C and the temperature at the top of the tower is 60°C. A very small amount of water (6kg / h) is separated as dilute hydrochloric acid into the dilute hydrochloric acid storage tank. The liquid in the bott...
PUM
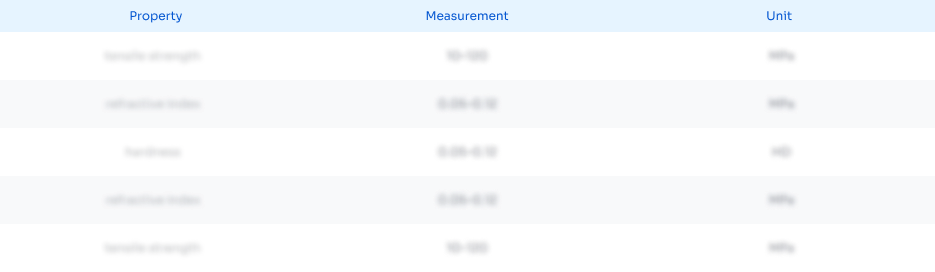
Abstract
Description
Claims
Application Information

- Generate Ideas
- Intellectual Property
- Life Sciences
- Materials
- Tech Scout
- Unparalleled Data Quality
- Higher Quality Content
- 60% Fewer Hallucinations
Browse by: Latest US Patents, China's latest patents, Technical Efficacy Thesaurus, Application Domain, Technology Topic, Popular Technical Reports.
© 2025 PatSnap. All rights reserved.Legal|Privacy policy|Modern Slavery Act Transparency Statement|Sitemap|About US| Contact US: help@patsnap.com