Gear grinding method
A gear and grinding technology, which is applied to gear tooth manufacturing devices, grinding/polishing equipment, belts/chains/gears, etc., can solve the problems of waste of grinding action and loss of processing time, and achieve the prevention of grinding burns and processing Effect of Accuracy Improvement
- Summary
- Abstract
- Description
- Claims
- Application Information
AI Technical Summary
Problems solved by technology
Method used
Image
Examples
Embodiment Construction
[0031] Hereinafter, the gear grinding method of the present invention will be described in detail using the drawings.
[0032] 【Example】
[0033] Such as figure 1 As shown, the rotary table 21 is mounted rotatably about a vertical workpiece axis of rotation C on the gear grinding wheel 1 . Further, a detachable workpiece (gear to be measured, gear to be processed) W is mounted on the upper surface of the rotary table 21 . Therefore, the workpiece W can be rotated around the workpiece rotation axis C by driving the rotary table 21 .
[0034] In addition, the grinding wheel head 11 is provided on the gear grinding table 1 so as to face the rotary table 21 . Further, the grinding wheel head 11 is supported so as to be movable along the X-axis, Y-axis, and Z-axis directions which represent the orthogonal three-axis directions of front-rear, left-right, and up-down, and to be rotatable about a horizontal grinding wheel turning axis A.
[0035] On the front surface of the grindi...
PUM
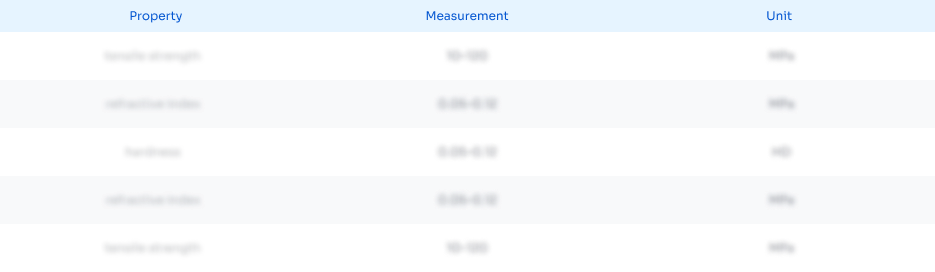
Abstract
Description
Claims
Application Information

- R&D
- Intellectual Property
- Life Sciences
- Materials
- Tech Scout
- Unparalleled Data Quality
- Higher Quality Content
- 60% Fewer Hallucinations
Browse by: Latest US Patents, China's latest patents, Technical Efficacy Thesaurus, Application Domain, Technology Topic, Popular Technical Reports.
© 2025 PatSnap. All rights reserved.Legal|Privacy policy|Modern Slavery Act Transparency Statement|Sitemap|About US| Contact US: help@patsnap.com