Preparation method of carbon cladding modified lithium manganate anode material
A technology of carbon-coated lithium manganate and lithium manganate, which is applied in the field of preparation of carbon-coated modified lithium manganate cathode materials, can solve the problems of unfavorable large-scale industrial production and high equipment requirements, and achieve good cycle life , Improve surface chemistry, improve electrical conductivity
- Summary
- Abstract
- Description
- Claims
- Application Information
AI Technical Summary
Problems solved by technology
Method used
Image
Examples
Embodiment 1
[0022] 1) The spinel LiMn 2 o 4 Weigh 100g of the powder and add it to 200ml of deionized water, stir magnetically, and mix evenly.
[0023] 2) Add 15 g of polyvinyl alcohol accounting for 15% by mass of the lithium manganate powder to the obtained mixed liquid, stir and mix evenly.
[0024] 3) Add 0.15 g of manganocene with a mass ratio of 1% of polyvinyl alcohol to the obtained mixed liquid, stir with an emulsifier until emulsified, and mix evenly.
[0025] 4) The obtained mixed solution is sprayed and granulated by a spray dryer to obtain lithium manganate powder evenly coated with organic carbon. The spray drying parameters are set as, the inlet temperature is 250°C, and the outlet temperature is 90°C.
[0026] 5) Put the obtained powder into a crucible, place in a tubular electric furnace, vacuumize, and pass nitrogen, repeat the process of vacuuming and nitrogen for 3 times, and heat at 450°C for 2 hours to obtain a carbon-coated lithium manganate cathode material.
...
Embodiment 2
[0029] 1) The spinel LiMn 2 o 4 Weigh 150g and add it into 400ml deionized water, stir and mix evenly.
[0030] 2) Add 15 g of sucrose accounting for 10% of the mass of lithium manganate powder to the obtained mixed liquid, stir and mix evenly.
[0031] 3) Add 0.45 g of cobaltocene, which accounts for 3% of the mass of sucrose, into the obtained mixed liquid, stir until emulsified state with an emulsifier, and mix evenly.
[0032] 4) The obtained mixed solution is sprayed and granulated by a spray dryer to obtain lithium manganate powder evenly coated with organic carbon. The parameters of spray drying are set as follows: the inlet temperature is 180°C, and the outlet temperature is 60°C.
[0033] 5) The obtained powder was put into a crucible, placed in a tubular electric furnace, evacuated, nitrogen-gassed, the process of vacuuming and nitrogen-gassed was repeated 3 times, and heated at 400°C for 4 hours to obtain a carbon-coated lithium manganate cathode material.
Embodiment 3
[0035] 1) The spinel LiMn 2 o 4 Weigh 200g and add it to 200ml deionized water, stir and mix evenly.
[0036] 2) Add 60 g of glucose accounting for 30% of the mass of the lithium manganate powder to the obtained mixed solution, stir and mix evenly.
[0037] 3) Add 1.8 g of manganese acetate accounting for 3% of the mass of glucose to the obtained mixed solution, stir, stir until emulsified state with an emulsifier, and mix evenly.
[0038] 4) The obtained mixed solution is sprayed and granulated by a spray dryer to obtain lithium manganate powder evenly coated with organic carbon. The spray drying parameters are set as follows: the inlet temperature is 220°C, the outlet temperature is 80°C, and the induced draft fan speed is set to 60%.
[0039] 5) The obtained powder was put into a crucible, placed in a microwave oven, evacuated, nitrogen-filled, repeated 3 times, and heated at 300° C. for 0.5 h to obtain a carbon-coated lithium manganate cathode material.
PUM
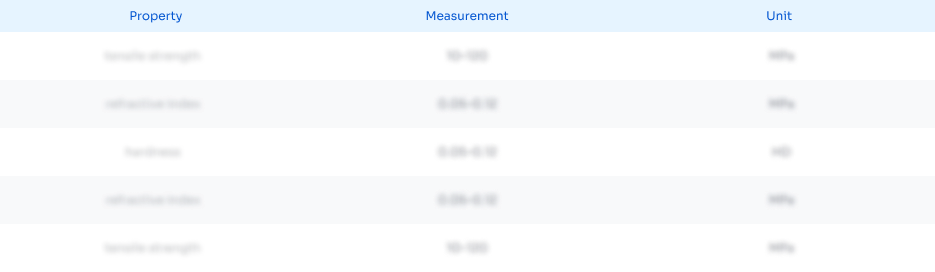
Abstract
Description
Claims
Application Information

- Generate Ideas
- Intellectual Property
- Life Sciences
- Materials
- Tech Scout
- Unparalleled Data Quality
- Higher Quality Content
- 60% Fewer Hallucinations
Browse by: Latest US Patents, China's latest patents, Technical Efficacy Thesaurus, Application Domain, Technology Topic, Popular Technical Reports.
© 2025 PatSnap. All rights reserved.Legal|Privacy policy|Modern Slavery Act Transparency Statement|Sitemap|About US| Contact US: help@patsnap.com