Surface mounting welding process for wafer-level chip
A surface mount and soldering process technology, which is applied in the direction of assembling printed circuits, electrical components, and electrical solid devices with electrical components, can solve the problems of low process cost reliability and high material, and achieve the goal of avoiding cost and process time Effect
- Summary
- Abstract
- Description
- Claims
- Application Information
AI Technical Summary
Problems solved by technology
Method used
Image
Examples
Embodiment 1
[0041] figure 1 , figure 2 As shown, in the bare crystal 10 used in the first embodiment, a metal electrode 11 for soldering is provided on the bottom surface of the bare crystal 10 .
[0042] Such as figure 2 and image 3 As shown, in the step of arranging, the bare crystals 10 are placed one by one into the temporary storage container 20 for storage. The temporary storage container 20 used in this embodiment has a linear braiding structure, and the elongated braiding is provided with multiple The accommodating spaces 23 are arranged in a straight line, each bare die 10 occupies one accommodating space 23 , and are independent from each other; and the metal electrodes 11 of the bare dies 10 all face the bottom of the accommodating spaces 23 . When the bare crystal 10 is placed into the accommodating space 23 , there will be a protective film 21 at the opening of the temporary storage container 20 to seal the accommodating space 23 for protection. The braiding has a posi...
Embodiment 2
[0056] Such as Figure 9 to Figure 12 , is a partial process diagram of Embodiment 2 of the present invention.
[0057] From Figure 9 It can be seen that the metal electrode of the die 10 has a portion extending on the side of the die 10, and, Figure 10 and Figure 11 It is shown that the temporary storage container 20 used by the bare die 10 is in the form of a tray, so the bare die 10 is distributed in the accommodation space 23 of the temporary storage container 10 in an array, and its metal electrodes 11 are also oriented toward the container. bottom of the space.
[0058] The placement steps of this embodiment are the same as those of Embodiment 1, and Figure 12 shows that the solder paste 50 is not only interposed between the metal electrode 11 and the pad 31, but also has a part attached to the metal electrode 11 on the side of the bare crystal 10. This welding method has high mechanical strength and a large solder joint current. In particular, from Figure 12 ...
PUM
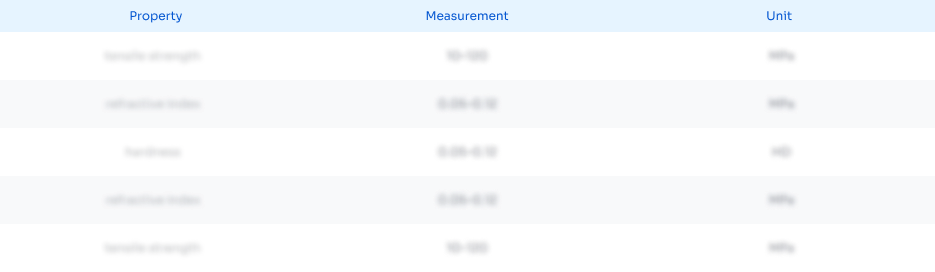
Abstract
Description
Claims
Application Information

- R&D
- Intellectual Property
- Life Sciences
- Materials
- Tech Scout
- Unparalleled Data Quality
- Higher Quality Content
- 60% Fewer Hallucinations
Browse by: Latest US Patents, China's latest patents, Technical Efficacy Thesaurus, Application Domain, Technology Topic, Popular Technical Reports.
© 2025 PatSnap. All rights reserved.Legal|Privacy policy|Modern Slavery Act Transparency Statement|Sitemap|About US| Contact US: help@patsnap.com