Automatic deashing device for thermal-powered or thermoelectric boilers
An automatic soot cleaning and boiler technology, which is applied in the fields of solid residue removal, lighting and heating equipment, combustion product treatment, etc., can solve the problem of not satisfying the soot blowing of large and medium-sized boilers, and does not play a role of local coordination and overall coordination , Can not adjust the radiation shape of the shock wave airflow, etc., to achieve the effect of preventing local deflagration, increasing energy intensity, and improving airflow
- Summary
- Abstract
- Description
- Claims
- Application Information
AI Technical Summary
Problems solved by technology
Method used
Image
Examples
Embodiment Construction
[0028] Such as figure 1 As shown, the structure and connection of the system of the present invention are as follows: the bottled acetylene gas in the gas source 5 constant pressure range is connected to the main gas pipeline 1002, and the main pipeline 1002 extends backwards to connect the gas inlet port of the fusion energy starter. A main control valve 7, a fire damper 8 and a check valve 9 are arranged on the pipeline 1003. The main pipeline 1002 is a round steel pipe with an outer diameter of 7mm to 194mm and a wall thickness ranging from 1mm to 50mm. The air source 6 pipeline leads The boiler air is connected to the main air pipeline 1001, and the main air pipeline 1001 extends backwards corresponding to the air inlet of the energy starter 1003 connected to the 1002, and the main control valve 7 and the inverter are set at 1001 between the air source 6 and the energy starter 1003. Stop valve 9. The main air pipeline 1001 is a round steel pipe with an outer diameter of 9...
PUM
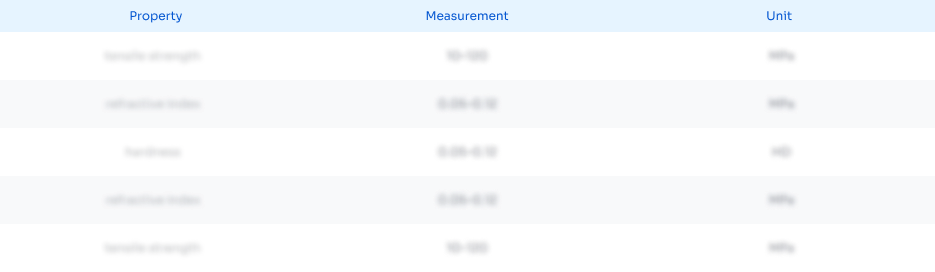
Abstract
Description
Claims
Application Information

- Generate Ideas
- Intellectual Property
- Life Sciences
- Materials
- Tech Scout
- Unparalleled Data Quality
- Higher Quality Content
- 60% Fewer Hallucinations
Browse by: Latest US Patents, China's latest patents, Technical Efficacy Thesaurus, Application Domain, Technology Topic, Popular Technical Reports.
© 2025 PatSnap. All rights reserved.Legal|Privacy policy|Modern Slavery Act Transparency Statement|Sitemap|About US| Contact US: help@patsnap.com