Method for preparing TC4 titanium alloy ingot casting through electron beam cold bed hearth smelting
An electron beam cooling hearth furnace and titanium alloy technology, which is applied in the field of titanium alloy ingot preparation, can solve the problems of large volatilization and difficult control of volatile alloy elements, and achieve the effects of reduced volatilization rate, easy breakage and improved utilization rate
- Summary
- Abstract
- Description
- Claims
- Application Information
AI Technical Summary
Problems solved by technology
Method used
Image
Examples
Embodiment 1
[0023] Step 1. Mix 0-grade titanium sponge and aluminum beans (mass purity: 99.6%) according to the mass ratio of 57:43, and then use a 500T hydraulic press to press it into an electrode block with a size of Φ50mm×300mm under the condition of a pressure not greater than 15MPa. Then, the four electrode blocks are welded by argon arc welding under the protection of argon gas, and the welding current is 300A. , under the condition that the smelting vacuum degree is not more than 14Pa, the smelting current is 1700A, and the smelting voltage is 30V, a brittle and easily broken Ti-Al master alloy is obtained by one smelting; the mass of Al in the aluminum bean is about the Ti-Al intermediate 1.02 times of Al quality in the alloy; The chemical composition of described Ti-Al master alloy is as shown in table 1:
[0024] Table 1 Chemical composition of Ti-Al master alloy
[0025]
[0026] Step 2, using a jaw crusher to crush the Ti-Al master alloy described in Step 1 into Ti-Al mas...
Embodiment 2
[0033]Step 1. Mix the grade 1 sponge titanium and aluminum beans (mass purity 99.8%) according to the mass ratio of 58:42, and then use a 500T hydraulic press to press it into an electrode block with a size of Φ50mm×300mm under the condition of a pressure not greater than 15MPa. Then, the three electrode blocks are welded by argon arc welding under the protection of argon gas and the welding current is 350A to form electrodes with a size of Φ50mm×900mm, and then the electrodes are placed in a 50kg vacuum consumable electric arc furnace , under the conditions that the smelting vacuum degree is not greater than 14Pa, the smelting current is 1600A, and the smelting voltage is 29V, a brittle and easily broken Ti-Al master alloy is obtained by one smelting; the quality of Al in the aluminum bean is Ti-Al master alloy 1.03 times of Al quality in the middle; The chemical composition of described Ti-Al master alloy is as shown in table 3:
[0034] Table 3 Chemical composition of Ti-Al...
Embodiment 3
[0043] Step 1. Mix 0-grade titanium sponge and aluminum beans (mass purity 99.6%) according to the mass ratio of 59:41, and then use a 500T hydraulic press to press it into an electrode block with a size of Φ50mm×300mm under the condition of a pressure not greater than 15MPa. Then, the four electrode blocks were welded into electrodes with a size of Φ50mm×1200mm under the protection of argon gas by argon arc welding and the welding current was 250A, and then the electrodes were placed in a vacuum consumable arc furnace. Under the condition that the smelting vacuum degree is not more than 14Pa, the smelting current is 1800A, and the smelting voltage is 30V, a brittle and easily broken Ti-Al master alloy is obtained by one smelting; 1.016 times of Al quality; The chemical composition of described Ti-Al master alloy is as shown in table 5:
[0044] Table 5 Chemical composition of Ti-Al master alloy
[0045]
[0046] Step 2, using a jaw crusher to crush the Ti-Al master alloy ...
PUM
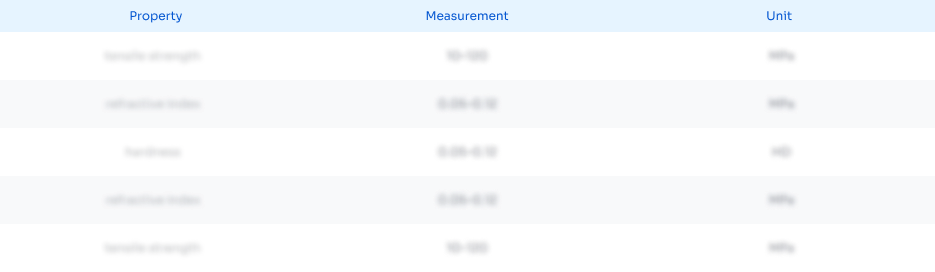
Abstract
Description
Claims
Application Information

- R&D
- Intellectual Property
- Life Sciences
- Materials
- Tech Scout
- Unparalleled Data Quality
- Higher Quality Content
- 60% Fewer Hallucinations
Browse by: Latest US Patents, China's latest patents, Technical Efficacy Thesaurus, Application Domain, Technology Topic, Popular Technical Reports.
© 2025 PatSnap. All rights reserved.Legal|Privacy policy|Modern Slavery Act Transparency Statement|Sitemap|About US| Contact US: help@patsnap.com