Selective hydrogenation method for C5 fraction of ethylene cracking by-product
An ethylene cracking and by-product technology, applied in the chemical industry, can solve the problems of low content of diolefins, high content of monoolefins, easy coke formation, etc.
- Summary
- Abstract
- Description
- Claims
- Application Information
AI Technical Summary
Problems solved by technology
Method used
Examples
Embodiment 1~ Embodiment 7
[0036] The catalyst used in the reaction is LHC1-01; the reactor is an adiabatic reactor. In order to make the temperature of the reaction bed uniform, the catalyst is loaded by stage dilution. According to the flow direction of the reactant, the volume consumption of each section of catalyst in Examples 1 to 4 is successively: 15%, 30%, 55%, and the catalyst loading is 100ml; the volume consumption of each section of catalyst in Examples 5 to 7 is successively: 10%, 15%. %, 25%, 50%, the catalyst loading is 100ml. The reaction raw material is C in the process of ethylene production 5 Raffinate, diluent and C 5 The ratio of the two is C 5 : Diluent volume ratio = 1:2; C 5 The composition of the raffinate is shown in Table 4. The reaction is upper feeding, the reaction material flows out from the bottom of the reactor, and enters the gas-liquid separator after cooling, the tail gas is discharged from the top of the separator, and the liquid phase at the bottom is regularly...
Embodiment 8
[0044] For a catalyst to have industrial application value, in addition to having good conversion rate and selectivity, it must also have good stability. The catalyst used in the reaction is LHC1-01; the reaction process is an adiabatic reactor. In order to make the temperature of the reaction bed uniform, the catalyst is loaded by stage dilution. According to the flow direction of the reactants, the catalyst volume consumption in each stage is as follows: 10%, 15%, 25%, 50%, and the catalyst loading is 100ml. The reaction raw material is C 5 Raffinate, diluent and C 5 The ratio of the two is C 5 : diluent = 1:2; C 5 The raffinate composition is the same as Table 4 in Example 1. The reaction is upper feed, the reaction material flows out from the bottom of the reactor, and enters the gas-liquid separator after cooling, the tail gas is discharged from the top of the separator, and the liquid phase at the bottom is regularly sampled, and the composition is analyzed by gas c...
Embodiment 9
[0049] The catalyst used in the reaction is LHC1-01; the reaction process is an adiabatic reactor. In order to make the temperature of the reaction bed uniform, the catalyst is loaded by stage dilution. According to the flow direction of the reactants, the catalyst volume consumption in each stage is as follows: 10%, 15%, 25%, 50%, and the catalyst loading is 100ml. The reaction raw material is C with high content of dicyclopentadiene 5 Raw materials, diluents and C 5 The ratio of the two is C 5 : diluent = 1:5; see Table 7 for raw material composition, diluent is C 5 mixed alkanes. The reaction is upper feeding, the reaction material flows out from the bottom of the reactor, and enters the gas-liquid separator after cooling, the tail gas is discharged from the top of the separator, and the liquid phase at the bottom is regularly sampled, and the composition is analyzed by gas chromatography. The specific reaction conditions and results are listed in Table 8.
[0050] ...
PUM
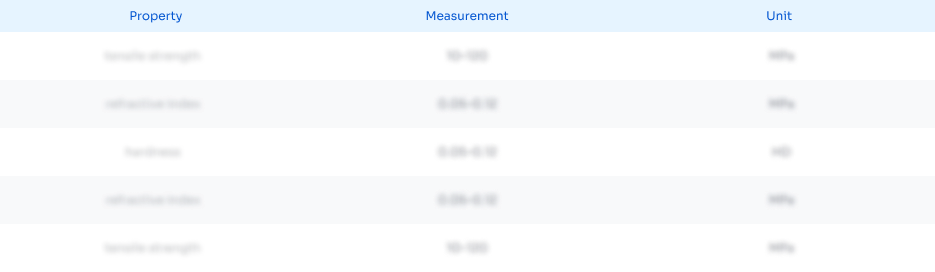
Abstract
Description
Claims
Application Information

- R&D Engineer
- R&D Manager
- IP Professional
- Industry Leading Data Capabilities
- Powerful AI technology
- Patent DNA Extraction
Browse by: Latest US Patents, China's latest patents, Technical Efficacy Thesaurus, Application Domain, Technology Topic, Popular Technical Reports.
© 2024 PatSnap. All rights reserved.Legal|Privacy policy|Modern Slavery Act Transparency Statement|Sitemap|About US| Contact US: help@patsnap.com