Manufacturing method for terylene strengthened filament weaving pattern rubber bottom coiled material
A manufacturing method and a technology for reinforcing filaments are applied in the field of coil manufacturing, which can solve the problems of radiation, dirt storage, poor foot feel, etc., and achieve the effects of good dimensional stability, no formaldehyde, and rich patterns.
- Summary
- Abstract
- Description
- Claims
- Application Information
AI Technical Summary
Problems solved by technology
Method used
Image
Examples
Embodiment 1
[0030] A method for manufacturing a polyester reinforced silk braided rubber base coil, comprising the following steps:
[0031] (1) The high-strength polyester yarn is warped to form a multi-strand monomer 500D, and then the PVC paste is plasticized. The formula is: polyvinyl chloride paste resin 100, dioctyl phthalate 100, 200 solvent oil 12, carbonic acid Calcium 20, appropriate amount of color paste, stabilizer 3. Then enter the 24M infrared oven for drying and plasticizing. (Temperature 170, 190, 170°C) cooled by refrigerated water, the water temperature is less than 18°C, and the warp is collected by the large shaft again, divided into warp and weft. Then it is spun on a projectile machine, which can produce weaving patterns of different colors and densities.
[0032] (2) Make adhesive: 100% vinyl acetate resin, 70% dioctyl phthalate, 5% cross-linking agent, 1 accelerator, pour into the high-speed disperser, stir at 1400r / min for 7 minutes, filter with a 100-mesh filte...
Embodiment 2
[0037] A method for manufacturing a polyester reinforced silk braided rubber base coil, comprising the following steps:
[0038] (1) Surface layer processing: The interior is made of high-strength polyester yarn through warping to form a multi-strand monomer, the exterior is coated with PVC paste and plasticized, and then enters a 24M infrared oven for drying, plasticizing, cooling at 170 ° C, and then It is spun by a projectile machine to obtain woven surface layers of different colors and densities. Among them, the PVC paste formula includes the following components and contents: polyvinyl chloride paste resin 100kg, dioctyl phthalate 100kg, 200 No. solvent oil 12kg, calcium carbonate 20, color paste heat-resistant purple 3kg, Ca / Zn composite heat stabilizer 3kg;
[0039] (2) Making adhesive: mix 100kg of vinyl acetate resin, 70kg of dioctyl phthalate, 5kg of cross-linking agent dicumyl peroxide, and 1kg of accelerator 2-mercaptobenzothiazole and place in high-speed dispersi...
Embodiment 3
[0044] A method for manufacturing a polyester reinforced silk braided rubber base coil, comprising the following steps:
[0045] (1) Surface layer processing: The interior is made of high-strength polyester yarns through warping to form multi-strand monomers, the exterior is coated with PVC paste and plasticized, and then enters a 24M infrared oven for drying, plasticizing, cooling at 190°C, and then It is spun by a projectile machine to obtain woven surface layers of different colors and densities. Among them, the PVC paste formula includes the following components and contents: polyvinyl chloride paste resin 100kg, dioctyl phthalate 100kg, 200 No. solvent oil 12kg, calcium carbonate 20, color paste organic perylene red 3kg, Ba / Zn composite heat stabilizer 3kg;
[0046] (2) Making adhesive: 100kg of vinyl chloride resin, 70kg of dioctyl phthalate, 5kg of crosslinking agent dicumyl hydroperoxide, and 1kg of accelerator N-cyclohexyl-2-benzothiazole sulfenamide After mixing, pl...
PUM
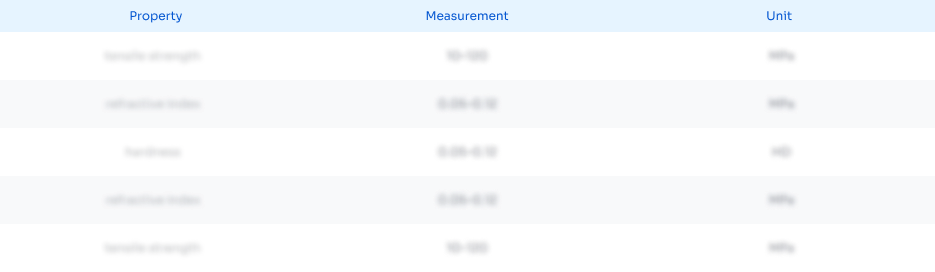
Abstract
Description
Claims
Application Information

- Generate Ideas
- Intellectual Property
- Life Sciences
- Materials
- Tech Scout
- Unparalleled Data Quality
- Higher Quality Content
- 60% Fewer Hallucinations
Browse by: Latest US Patents, China's latest patents, Technical Efficacy Thesaurus, Application Domain, Technology Topic, Popular Technical Reports.
© 2025 PatSnap. All rights reserved.Legal|Privacy policy|Modern Slavery Act Transparency Statement|Sitemap|About US| Contact US: help@patsnap.com