Hall position sensor-based position estimation and compensation method for permanent magnet synchronous motor
A technology of permanent magnet synchronous motor and Hall position, which is applied in the direction of torque ripple control, etc., can solve the problems of installation accuracy, symmetry, and error, and achieve the effect of reducing torque ripple and noise, and reducing waveform distortion
- Summary
- Abstract
- Description
- Claims
- Application Information
AI Technical Summary
Problems solved by technology
Method used
Image
Examples
Embodiment Construction
[0027] In order to make the technical problems, technical solutions and beneficial effects solved by the present invention clearer, the present invention will be further described in detail below in conjunction with the contributions and examples.
[0028] 1. Define the interval number i of the three-phase Hall position signal and the initial angle value of the interval, such as figure 1 As shown, set the ABC three-phase Hall signal to be 1 when the level is high, and to be 0 when the level is low.
[0029] ABC=101: i=1, interval initial angle value: 0°
[0030] ABC=100: i=2, interval initial angle value: 60°
[0031] ABC=110: i=3, interval initial angle value: 120°
[0032] ABC=010: i=4, interval initial angle value: 180°
[0033] ABC=011: i=5, interval initial angle value: 240°
[0034] ABC=001: i=6, interval initial angle value: 300°
[0035]2. Drive the open-loop permanent magnet synchronous motor to run at a fixed speed with a VVVF constant voltage-frequency r...
PUM
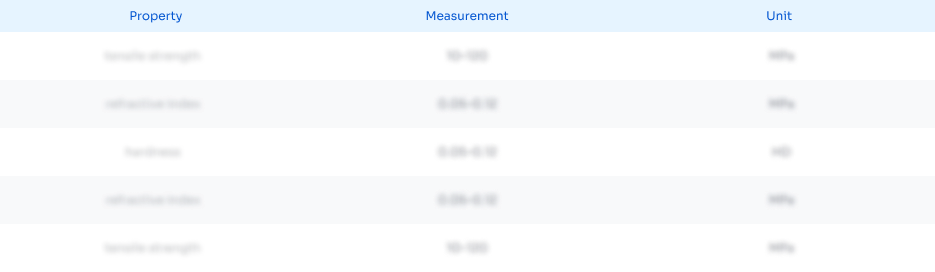
Abstract
Description
Claims
Application Information

- R&D
- Intellectual Property
- Life Sciences
- Materials
- Tech Scout
- Unparalleled Data Quality
- Higher Quality Content
- 60% Fewer Hallucinations
Browse by: Latest US Patents, China's latest patents, Technical Efficacy Thesaurus, Application Domain, Technology Topic, Popular Technical Reports.
© 2025 PatSnap. All rights reserved.Legal|Privacy policy|Modern Slavery Act Transparency Statement|Sitemap|About US| Contact US: help@patsnap.com