Acceleration frequency response analysis-based body floor optimal design method
A frequency response, body floor technology, applied in the field of body floor optimization design based on acceleration frequency response analysis, can solve the problems of no error control, unable to optimize the design of body floor, etc., to achieve pleasant sound, shorten development time, and reduce errors.
- Summary
- Abstract
- Description
- Claims
- Application Information
AI Technical Summary
Problems solved by technology
Method used
Image
Examples
Embodiment Construction
[0037] The present invention will be further described below in conjunction with the accompanying drawings and specific embodiments.
[0038] Such as figure 1 The illustrated embodiment is a method for optimal design of a vehicle body floor based on acceleration frequency response analysis, including the following steps:
[0039] (1) According to the body shape and body layout data, obtain the input conditions of the body floor design;
[0040] (2) Carry out preliminary structural design for the body floor according to the design input conditions, and establish a CAD model through CATIA software;
[0041] (3) Carry out grid division on the established CAD model, and establish the finite element model of the body-in-white; figure 2 The finite element model shown. The specific process is:
[0042] Import the CAD model into the finite element pre-processing software with CAD structure, and the pre-processing software can use Hypermesh;
[0043] The data is divided into grid...
PUM
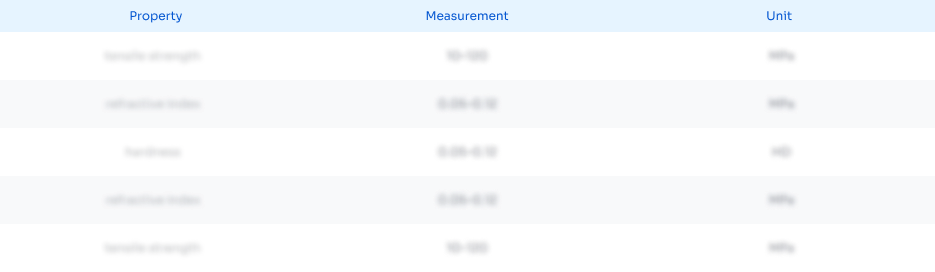
Abstract
Description
Claims
Application Information

- R&D
- Intellectual Property
- Life Sciences
- Materials
- Tech Scout
- Unparalleled Data Quality
- Higher Quality Content
- 60% Fewer Hallucinations
Browse by: Latest US Patents, China's latest patents, Technical Efficacy Thesaurus, Application Domain, Technology Topic, Popular Technical Reports.
© 2025 PatSnap. All rights reserved.Legal|Privacy policy|Modern Slavery Act Transparency Statement|Sitemap|About US| Contact US: help@patsnap.com