Target shape optimization method for aspherical optical element in conventional processing stage
An optical component, traditional processing technology, applied in the direction of optical components, optics, instruments, etc., can solve the problem of excessive removal of workpiece surface, excessive surface shape error of intermediate frequency, large deviation between near spherical and aspherical surfaces, etc.
- Summary
- Abstract
- Description
- Claims
- Application Information
AI Technical Summary
Problems solved by technology
Method used
Image
Examples
Embodiment Construction
[0059] Such as figure 2 , image 3 As shown, the concave off-axis parabolic mirror 1 is located on the parabolic surface 2 of revolution. P 1 P n It is the intercept curve obtained by intersecting the xoy plane, O i Point at P i The normal of the point. figure 2 The positional relationship between the concave off-axis parabolic mirror 1 and the paraboloid of revolution 2 is shown as a whole. The equation of concave off-axis parabolic mirror 1 is y 2 +z 2 =2400x, y∈[42,143], z∈[-50,50], the units are all millimeters.
[0060] Usually a laser interferometer is used to measure the surface shape of the workpiece. Since the resolution of the interferometer's lateral measurement is 0.1 to 0.2 mm, when the surface equation is discretized in the computer, the y direction of the two adjacent points of the data point matrix The distance from the z direction is set to 0.1 mm, and Δr=0.1 mm.
[0061] The value of n and m determines the accuracy of the calculation. Here, we choose n=1000, m...
PUM
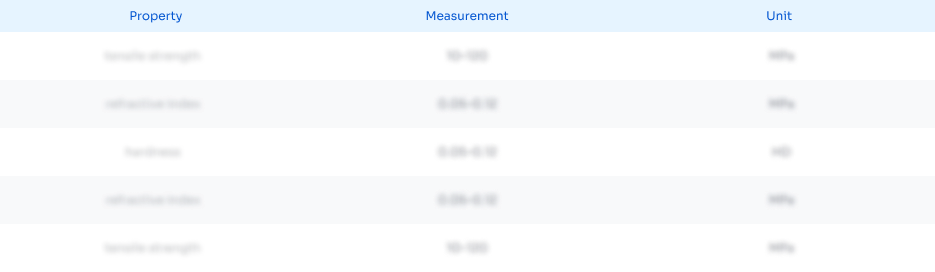
Abstract
Description
Claims
Application Information

- Generate Ideas
- Intellectual Property
- Life Sciences
- Materials
- Tech Scout
- Unparalleled Data Quality
- Higher Quality Content
- 60% Fewer Hallucinations
Browse by: Latest US Patents, China's latest patents, Technical Efficacy Thesaurus, Application Domain, Technology Topic, Popular Technical Reports.
© 2025 PatSnap. All rights reserved.Legal|Privacy policy|Modern Slavery Act Transparency Statement|Sitemap|About US| Contact US: help@patsnap.com