Manufacturing method of melt direct spinning high-performance heterotypic polyester fiber
A manufacturing method and polyester fiber technology, which are applied in the directions of single-component polyester rayon filament, fiber processing, rayon manufacturing, etc., can solve the problems of little research on the properties of special-shaped polyester fibers and many researches on technology, and achieve The effect of solving the problem of oiling, reducing the hairiness of special-shaped silk, and improving the stretchability
- Summary
- Abstract
- Description
- Claims
- Application Information
AI Technical Summary
Problems solved by technology
Method used
Image
Examples
Embodiment 1
[0021] The manufacture method of embodiment 1 hollow profiled fiber
[0022] At present, the high-end hollow fiber varieties on the market are of poor quality, especially the hollowness is not high, the dyeability is not good, and the processing performance is poor. Embodiment 1 has made a breakthrough and innovation especially in the selection of the spinneret spinneret holes. The concrete steps of embodiment 1 are as follows.
[0023] 1) Select the polyester melt added with pentaerythritol, and transport it to the spinning assembly through the pipeline delivery system.
[0024] 2) The polyester melt is sprayed out through the spinneret holes in the spinning assembly. The hollowness of the spinneret micropores is more than 60%, and the spinneret plate diameter is 100mm, forming multiple single filament streams.
[0025] Because the special-shaped spinneret hole method is used to make the fine flow of the melt expand through the outlet, bond and cool and solidify to form a...
Embodiment 2 10
[0039] The manufacture method of embodiment 2 cross shaped fibers
[0040] like figure 1 , figure 2 and image 3 As shown, the cross-shaped spinneret has been developed to the third generation so far, and the cross shape of the first-generation cross-shaped spinneret is a positive cross ( figure 1 ), the cross shape of the second-generation cross-shaped spinneret is two dumbbells intersecting into a cross ( figure 2 ), the cross shape of the third-generation cross-shaped spinneret is a hammer-like cross into a cross ( image 3 ). At present, most of the spinnerets of cross shaped fibers are stuck in the first generation and the second generation.
Embodiment 2
[0041] Embodiment 2 innovatively adopts the third-generation cross-shaped spinneret, that is, the cross-shaped spinneret imitating the hammer shape is used for spinning. Specific steps are as follows.
[0042] 1) Select the polyester melt added with pentaerythritol, and transport it to the spinning assembly through the pipeline delivery system.
[0043] 2) The polyester melt is sprayed out through the spinneret hole in the spinning assembly, and the selected spinneret is a hammer-shaped cross-shaped spinneret.
[0044] 3) Uniformly cool the monofilament stream through the ring blowing to form a solid monofilament.
[0045] 4) Multi-strand solid monofilaments are bundled into multifilaments through oil nozzles, and the multifilaments are formed by winding.
[0046] The cross-shaped shaped fiber produced in Example 2 has greatly improved its moisture absorption and dyeing effects through tests. The contrast effect is as follows figure 1 and shown in Table 4.
[0047] like fi...
PUM
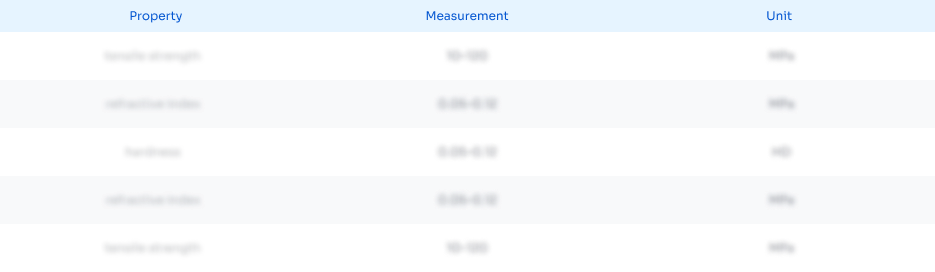
Abstract
Description
Claims
Application Information

- R&D
- Intellectual Property
- Life Sciences
- Materials
- Tech Scout
- Unparalleled Data Quality
- Higher Quality Content
- 60% Fewer Hallucinations
Browse by: Latest US Patents, China's latest patents, Technical Efficacy Thesaurus, Application Domain, Technology Topic, Popular Technical Reports.
© 2025 PatSnap. All rights reserved.Legal|Privacy policy|Modern Slavery Act Transparency Statement|Sitemap|About US| Contact US: help@patsnap.com