Method for reducing X20Cr13 longitudinal and transverse mechanical property differences
A x20cr13, vertical and horizontal technology, applied in the field of stainless steel materials, can solve problems such as differences in mechanical properties, and achieve the effect of reducing vertical and horizontal performance differences and improving vertical and horizontal mechanical properties
- Summary
- Abstract
- Description
- Claims
- Application Information
AI Technical Summary
Problems solved by technology
Method used
Image
Examples
Embodiment 1
[0018] In this example, we take the following steps:
[0019] Take the required elements containing the following parts by weight: C 0.17; Si 0.10; Mn 0.30; Ni 0.30;
[0020] Add rare earth element cerium in the smelting process, the content of rare earth element cerium accounts for 0.042% by weight of the total weight, control the content of impurity elements as low as possible, and pour the solution into a consumable electrode;
[0021] The consumable electrode is remelted and refined in the electroslag furnace, and the melting speed is controlled at 4.0~5.0Kg / min. While further reducing the content of impurity elements, the properties of inclusions and the directionality of crystallization are changed as much as possible to make electroslag heavy Ingot;
[0022] The electroslag remelting ingot is rounded as a whole;
[0023] The press performs three upsetting and drawing processes, and the deformation of each upsetting is ≥45%;
[0024] The finished forging adopts cross ...
Embodiment 2
[0027] In this example, we take the following steps:
[0028] Take the required elements containing the following parts by weight: C 0.19; Si 0.25; Mn 0.45; Ni 0.40;
[0029] Add rare earth element cerium in the smelting process, the content of rare earth element cerium accounts for 0.043% by weight of the total weight, control the content of impurity elements as low as possible, and pour the solution into a consumable electrode;
[0030] The consumable electrode is remelted and refined in the electroslag furnace, and the melting speed is controlled at 4.0~5.0Kg / min. While further reducing the content of impurity elements, the properties of inclusions and the directionality of crystallization are changed as much as possible to make electroslag heavy Ingot;
[0031] The electroslag remelting ingot is rounded as a whole;
[0032] The press performs three upsetting and drawing processes, and the deformation of each upsetting is ≥45%;
[0033] The finished forging adopts cross ...
Embodiment 3
[0036] In this example, we take the following steps:
[0037] Take the required elements containing the following parts by weight: C 0.20; Si 0.35; Mn 0.50; Ni 0.50; Cr 13.5, and initially smelt in a non-vacuum induction furnace at a melting temperature of 1520~1620°C;
[0038] Add rare earth element cerium in the smelting process, the content of rare earth element cerium accounts for 0.044% by weight of the total weight, control the content of impurity elements as low as possible, and pour the solution into a consumable electrode;
[0039] The consumable electrode is remelted and refined in the electroslag furnace, and the melting speed is controlled at 4.0~5.0Kg / min. While further reducing the content of impurity elements, the properties of inclusions and the directionality of crystallization are changed as much as possible to make electroslag heavy Ingot;
[0040] The electroslag remelting ingot is rounded as a whole;
[0041] The press performs three upsetting and drawin...
PUM
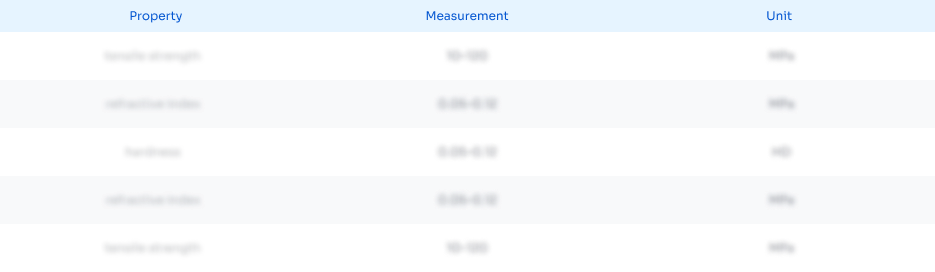
Abstract
Description
Claims
Application Information

- Generate Ideas
- Intellectual Property
- Life Sciences
- Materials
- Tech Scout
- Unparalleled Data Quality
- Higher Quality Content
- 60% Fewer Hallucinations
Browse by: Latest US Patents, China's latest patents, Technical Efficacy Thesaurus, Application Domain, Technology Topic, Popular Technical Reports.
© 2025 PatSnap. All rights reserved.Legal|Privacy policy|Modern Slavery Act Transparency Statement|Sitemap|About US| Contact US: help@patsnap.com