Composite oxide oxygen carrier and preparation method and application thereof
A composite oxide, oxygen carrier technology, applied in chemical instruments and methods, metal/metal oxide/metal hydroxide catalysts, chemical/physical processes, etc., can solve the problem of low dispersion of metal oxides and cyclic reactivity Low oxygen carrying rate, limited oxygen carrying rate, etc., to achieve the effect of improving oxygen carrying rate and activity, high activity and low cost
- Summary
- Abstract
- Description
- Claims
- Application Information
AI Technical Summary
Problems solved by technology
Method used
Image
Examples
Embodiment 1
[0019] Take 23gCo(NO 3 ) 2 ﹒ 6H 2 Put O into a 500mL beaker, add 100mL of distilled water, then place the beaker in a water bath at 80°C, stir at 400rpm, and stir until completely dissolved. Take 30.87g La(NO 3 ) 3 ﹒ 6H 2 O and 0.8g KNO 3 Put it into a beaker with 100mL of distilled water and stir until it is completely dissolved so that the molar ratio of La to K is 0.9 / 0.1. Then add the lanthanum nitrate and potassium nitrate solutions dropwise to the cobalt nitrate solution, and stir while adding. Take 40g of citric acid, the molar ratio of citric acid to the total amount of metal ions is 1.2:1, put it into a 100mL beaker and stir until it is completely dissolved. At this time, after the above mixed solution is stirred for 30 minutes, slowly add the citric acid solution, while Add dropwise while stirring. After stirring for 5 hours, the brown solution had been dehydrated and turned into a viscous gel. The gel was taken out and placed in a drying oven at 110° C. to...
Embodiment 2
[0021] Take 23gCo(NO 3 ) 2 ﹒ 6H 2 Put O into a 500mL beaker, add 100mL of distilled water, then place the beaker in a water bath at 80°C, stir at 400rpm, and stir until completely dissolved. Take 29.15g La(NO 3 ) 3 ﹒ 6H 2 O and 1.2g KNO 3 Put it into a beaker with 100mL of distilled water, stir until it is completely dissolved, so that the molar ratio of La to K is 0.85 / 0.15. Then add the lanthanum nitrate and potassium nitrate solutions dropwise to the cobalt nitrate solution, and stir while adding. Take 67g of citric acid, the molar ratio of citric acid to metal ions is 1.2:1, put it into a 100mL beaker and stir until it is completely dissolved. After the above mixed solution is stirred for 30 minutes, slowly add the citric acid solution, while adding While stirring. After stirring for 5 hours, the brown solution had been dehydrated and turned into a viscous gel. The gel was taken out and placed in a drying oven at 110° C. to dry overnight. Then take out the dried...
Embodiment 3
[0023] Take 23gCo(NO 3 ) 2 ﹒ 6H 2 Put O into a 500mL beaker, add 100mL of distilled water, then place the beaker in a water bath at 80°C, stir at 400rpm, and stir until completely dissolved. Take 27.44g La(NO 3 ) 3 ﹒ 6H 2 O and 1.6g KNO 3 Put it into a beaker with 100mL of distilled water and stir until it is completely dissolved so that the molar ratio of La to K is 0.8 / 0.2. Then add the lanthanum nitrate and potassium nitrate solutions dropwise to the cobalt nitrate solution, and stir while adding. Take 40g of citric acid, the molar ratio of citric acid to the total amount of metal ions is 1.2:1, put it into a 100mL beaker and stir until it is completely dissolved. After the above mixed solution is stirred for 30 minutes, slowly add the citric acid solution, while adding While stirring. After stirring for 5 hours, the brown solution had been dehydrated and turned into a viscous gel. The gel was taken out and placed in a drying oven at 110° C. to dry overnight. The...
PUM
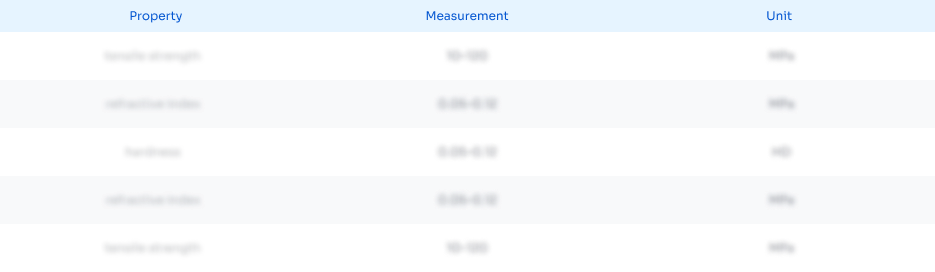
Abstract
Description
Claims
Application Information

- R&D Engineer
- R&D Manager
- IP Professional
- Industry Leading Data Capabilities
- Powerful AI technology
- Patent DNA Extraction
Browse by: Latest US Patents, China's latest patents, Technical Efficacy Thesaurus, Application Domain, Technology Topic, Popular Technical Reports.
© 2024 PatSnap. All rights reserved.Legal|Privacy policy|Modern Slavery Act Transparency Statement|Sitemap|About US| Contact US: help@patsnap.com