A heat recovery method for treating blast furnace slag
A technology of heat energy recovery and blast furnace slag, applied in waste heat treatment, energy efficiency improvement, furnace, etc., can solve environmental pollution and other problems, achieve high granulation efficiency, increase heat transfer surface area, and reduce particle size
- Summary
- Abstract
- Description
- Claims
- Application Information
AI Technical Summary
Problems solved by technology
Method used
Image
Examples
Embodiment
[0021] When the high-temperature blast furnace slag at a temperature of 1500°C enters the fluidized bed through the tank, the high-pressure air in the lower part of the tank blows the blast furnace slag melt to complete granulation; The cold slag meets and collides in the fluidized bed. The amount of cold slag sprayed by the cold slag nozzle at high speed accounts for 15% of the total amount of molten slag. The upward spraying angle of the cold slag nozzle is 35°. The bead flows are the same, forming an angle of 25° with each other; the slag particles after collision are violently mixed with cold air through the air distribution device for heat exchange, and the slag beads are cooled to 300°C; the cooled slag beads are used as cement raw materials, and the The vitreous body content reaches 95%, the heated heat exchange air enters the waste heat boiler, and the saturated steam generated by the waste heat boiler flows through the top of the fluidized bed for further heating, beco...
PUM
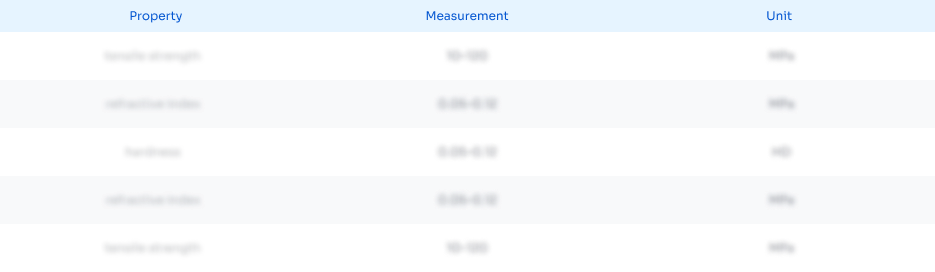
Abstract
Description
Claims
Application Information

- R&D Engineer
- R&D Manager
- IP Professional
- Industry Leading Data Capabilities
- Powerful AI technology
- Patent DNA Extraction
Browse by: Latest US Patents, China's latest patents, Technical Efficacy Thesaurus, Application Domain, Technology Topic, Popular Technical Reports.
© 2024 PatSnap. All rights reserved.Legal|Privacy policy|Modern Slavery Act Transparency Statement|Sitemap|About US| Contact US: help@patsnap.com