Double-switch magnetoresistive motor system based on synchronous drive
A technology of switched reluctance motor and reluctance motor, which is applied in multiple motor speed/torque control, electronic commutator, etc., and can solve the problems of increasing system cost and volume, synchronization error, and inability to achieve zero-error synchronization, etc.
- Summary
- Abstract
- Description
- Claims
- Application Information
AI Technical Summary
Problems solved by technology
Method used
Image
Examples
Embodiment Construction
[0032] In order to describe the present invention more specifically, the technical solutions and related principles of the present invention will be described in detail below in conjunction with the accompanying drawings and specific embodiments.
[0033] Such as Figure 4 As shown, a dual switched reluctance motor system based on synchronous drive, including: power converter, battery, position detector, controller, master switched reluctance motor and slave switched reluctance motor, two switched reluctance motors are It is a switched reluctance motor with a three-phase 12 / 8 structure, and the switched reluctance motor with this structure has three stator windings.
[0034] The position detector is used to detect and obtain the position status information of the rotor of the main switched reluctance motor; it is connected to the controller. The shaft of the encoder is connected to the shaft of the main motor. When connecting, align the zero mark of the encoder with the maxim...
PUM
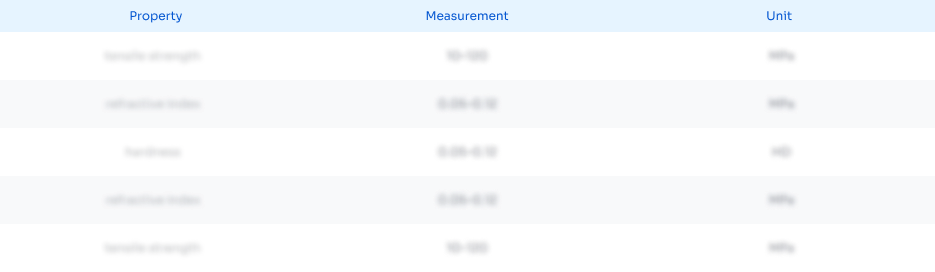
Abstract
Description
Claims
Application Information

- R&D
- Intellectual Property
- Life Sciences
- Materials
- Tech Scout
- Unparalleled Data Quality
- Higher Quality Content
- 60% Fewer Hallucinations
Browse by: Latest US Patents, China's latest patents, Technical Efficacy Thesaurus, Application Domain, Technology Topic, Popular Technical Reports.
© 2025 PatSnap. All rights reserved.Legal|Privacy policy|Modern Slavery Act Transparency Statement|Sitemap|About US| Contact US: help@patsnap.com