Circuit board testing system
A test system and circuit board technology, applied in the direction of electronic circuit testing, etc., can solve the problems of high degree of customization of test equipment, uneconomical investment, multiple test machines, etc., to eliminate the gap between untested circuit boards and tested circuit boards Possibility, improvement of product quality and effect of cost reduction
- Summary
- Abstract
- Description
- Claims
- Application Information
AI Technical Summary
Problems solved by technology
Method used
Image
Examples
Embodiment 1
[0042] see figure 1 , as shown in the illustration therein, a circuit board testing system comprising:
[0043] A grid-type cabinet frame 1; the grids are arranged to arrange four horizontally and stack three vertically;
[0044] Twelve box-type testing machines 2 are placed in the twelve grids of the grid-type cabinet frame 1;
[0045] A loading and unloading manipulator 3, used to put the circuit board 4 into the box-type testing machine 2 and take out the circuit board 4 from the box-type testing machine 2;
[0046] A control system includes a PC processor 5 and a PLC control system 6, the box-type testing machine is connected to the PC processor by communication, and the PC processor 5 is connected to the PLC control system 6 by communication, and the The PLC control system 6 communicates with the twelve box-type testing machines 2 and the loading and unloading manipulator 3 respectively.
[0047] A barcode scanning gun 7, the barcode scanning gun 7 scans the barcode of...
Embodiment 2
[0080] see Figure 1-Figure 7 , the rest are the same as in the first embodiment, the difference is that the circuit board testing system also includes a material delivery mechanism, and the material delivery mechanism includes:
[0081] A feeding conveyor belt 81, located on the ejecting side of the drawer fixture 22, for transferring the circuit board 41 to be tested;
[0082] A feeding conveyor belt 82 is arranged on the pop-up side of the drawer-type fixture 22, and is used to transfer the tested circuit board 42, and the feeding conveyor belt 82 is arranged above the feeding conveyor belt 81;
[0083] A loading positioning platform 9 is located at one end of the feeding conveyor belt 81 and is located in the same horizontal plane as the drawer fixture 22. The barcode scanning gun 7 is located on the loading positioning platform 9, and the loading The positioning platform 9 includes a platform, a baffle plate arranged on the platform, and a push cylinder arranged relative...
Embodiment 3
[0087] All the other are the same as the embodiment 2, the difference is that the material transmission mechanism includes a plurality of feeding conveyor belts 81, a plurality of unloading conveyor belts 82 and a plurality of back-shaped connection mechanisms, and the multiple feeding conveyor belts 81 pass through The loading and unloading platforms 9 are connected; the plurality of unloading conveyor belts 82 are connected through the loop connection mechanism.
PUM
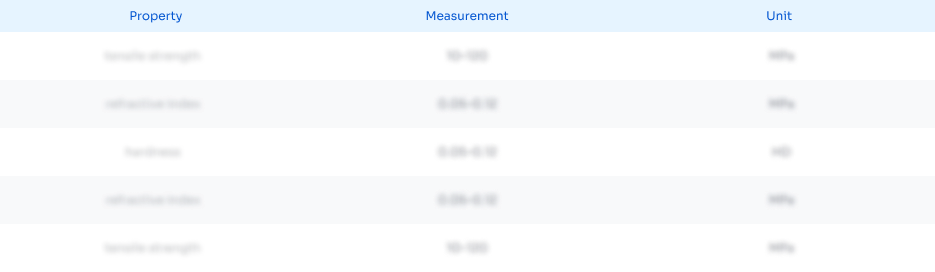
Abstract
Description
Claims
Application Information

- R&D
- Intellectual Property
- Life Sciences
- Materials
- Tech Scout
- Unparalleled Data Quality
- Higher Quality Content
- 60% Fewer Hallucinations
Browse by: Latest US Patents, China's latest patents, Technical Efficacy Thesaurus, Application Domain, Technology Topic, Popular Technical Reports.
© 2025 PatSnap. All rights reserved.Legal|Privacy policy|Modern Slavery Act Transparency Statement|Sitemap|About US| Contact US: help@patsnap.com