Pneumatic self-locking valve
A pneumatic, self-locking valve technology, applied in valve details, valve devices, engine components, etc., can solve problems such as inability to work for a long time, poor compatibility with corrosive working media, etc., to avoid contact and solve long-term and Compatibility problems with corrosive working medium, small volume effect
- Summary
- Abstract
- Description
- Claims
- Application Information
AI Technical Summary
Problems solved by technology
Method used
Image
Examples
Embodiment Construction
[0018] The present invention will be further elaborated below in conjunction with the accompanying drawings and specific embodiments. These examples should be understood as only for illustrating the present invention but not for limiting the protection scope of the present invention. After reading the contents of the present invention, those skilled in the art can make various changes or modifications to the present invention, and these equivalent changes and modifications also fall within the scope defined by the claims of the present invention.
[0019] Such as figure 1 As shown, the pneumatic self-locking valve provided by the preferred embodiment of the present invention is mainly composed of a filter 1, a first suction valve seat 2, a locking magnetic ring 3, a coil assembly 4, a piston 5, a compression nut 6, a housing 7. Plastic valve core 8, adjusting orifice plate assembly 9, imported welding nozzle 10, lock nut 11, piston shaft assembly 12, metal bellows 13, sealing...
PUM
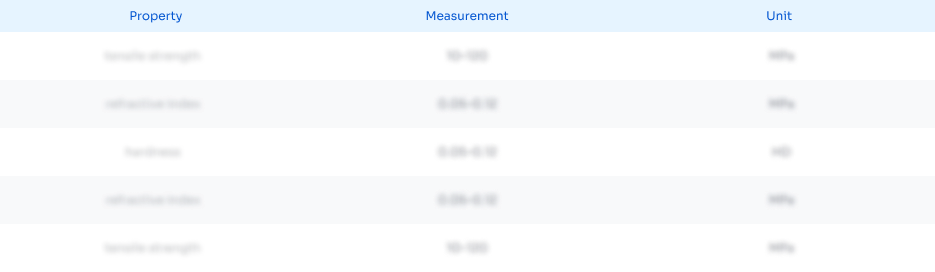
Abstract
Description
Claims
Application Information

- R&D
- Intellectual Property
- Life Sciences
- Materials
- Tech Scout
- Unparalleled Data Quality
- Higher Quality Content
- 60% Fewer Hallucinations
Browse by: Latest US Patents, China's latest patents, Technical Efficacy Thesaurus, Application Domain, Technology Topic, Popular Technical Reports.
© 2025 PatSnap. All rights reserved.Legal|Privacy policy|Modern Slavery Act Transparency Statement|Sitemap|About US| Contact US: help@patsnap.com