Double-throttle control slurry pump distributing manifold for applying wellhead back pressure and method
A mud pump and shunt pipe technology, which is applied in the field of double throttle control mud pump shunt manifold, can solve the problems of back pressure pump leakage pollution, non-production time increase, bottom hole pressure control inaccuracy, etc.
- Summary
- Abstract
- Description
- Claims
- Application Information
AI Technical Summary
Problems solved by technology
Method used
Image
Examples
Embodiment Construction
[0081] Such as figure 1 As shown, the diversion manifold of the mud pump with double throttling control includes the main pipe 1, the manifold cross 37, the first diversion line 2, the second diversion line 3 and the third diversion line 4; the manifold cross 37 is respectively connected to the main pipe 1 , the first shunt line 2, the second shunt line 3 and the third shunt line 4; the main pipe 1 is equipped with a pressure gauge 5; the first shunt line 2 is equipped with a first cut-off valve 6 and a first throttle valve 9, the first A shut-off valve 6 is located between the first throttling valve 9 and the manifold spool 37; a second shut-off valve 7 and a second throttling valve 10 are installed on the second branch line 3, and the second shut-off valve 7 is located in the second joint Between the flow valve 10 and the manifold spool 37; the third cut-off valve 8 is installed on the third diversion line 4. The diversion of the drilling fluid is realized by switching the ...
PUM
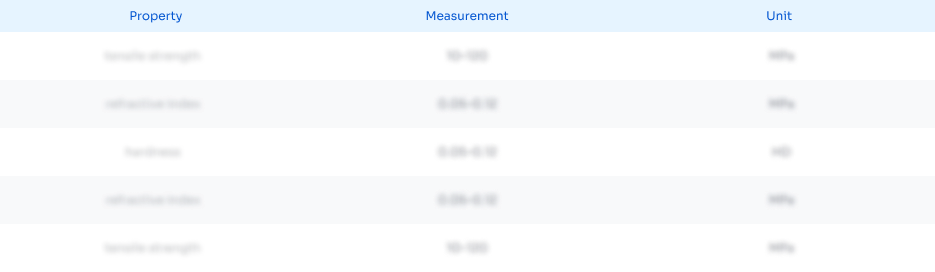
Abstract
Description
Claims
Application Information

- Generate Ideas
- Intellectual Property
- Life Sciences
- Materials
- Tech Scout
- Unparalleled Data Quality
- Higher Quality Content
- 60% Fewer Hallucinations
Browse by: Latest US Patents, China's latest patents, Technical Efficacy Thesaurus, Application Domain, Technology Topic, Popular Technical Reports.
© 2025 PatSnap. All rights reserved.Legal|Privacy policy|Modern Slavery Act Transparency Statement|Sitemap|About US| Contact US: help@patsnap.com