Prehydrolysis additive for dissolving pulp production and preparation method thereof
A technology of pre-hydrolysis and dissolving pulp, which is applied in the direction of pulping with acid acid/anhydride, which can solve the problems affecting the application of dissolving pulp and the high ash content of dissolving pulp, so as to protect from degradation, improve the removal rate, The effect of reducing the content
- Summary
- Abstract
- Description
- Claims
- Application Information
AI Technical Summary
Problems solved by technology
Method used
Examples
Embodiment 1
[0023] Weigh 10kg of fatty alcohol polyoxyethylene ether, 35kg of sodium bisulfite, 5kg of sodium hexametaphosphate, 5kg of oxalic acid, and 5kg of citric acid, and mix the above components uniformly at room temperature for 30 minutes to obtain the finished hydrolysis aid. It can leave the factory after discharging and bagging.
[0024] Bamboo slices from a paper mill in Sichuan were taken, and the analysis showed that the hemicellulose content was 21.68%, the ash content was 1.63%, and the lignin content was 25.45%. It was subjected to steam prehydrolysis, and the results are shown in Table 1.
[0025] Table 1 Contents of chemical components of tablets after prehydrolysis
[0026] Auxiliary dosage ( %) 0.0 0.5 0.7 1.0 Hemicellulose (to raw material) (%) 11.75 9.91 9.48 8.92 Hemicellulose removal rate (to raw material) (%) 45.80 54.29 56.27 58.86 Ash content (to raw materials) (%) 1.32 1.10 0.89 0.82 ...
Embodiment 2
[0030] Weigh 5kg fatty alcohol polyoxyethylene ether, 5kg alkylphenol polyoxyethylene ether, 35kg sodium bisulfite, 5kg sodium hexametaphosphate, 5kg oxalic acid, 5kg citric acid, and mix the above components uniformly at room temperature for 60 Minutes, it is the finished hydrolysis aid, and it can leave the factory after discharging and bagging.
[0031] Poplar wood chips from a paper mill in Henan were taken, and the analysis showed that the hemicellulose content was 23.19%, the ash content was 0.47%, and the lignin content was 18.22%. It was subjected to water prehydrolysis, and the results are shown in Table 2.
[0032] Table 2 Contents of chemical components of tablets after prehydrolysis
[0033] Auxiliary dosage ( %) 0.0 0.5 0.7 1.0 Hemicellulose (to raw material) (%) 12.37 10.62 9.78 8.61 Hemicellulose removal rate (to raw material) (%) 46.65 54.20 57.83 62.87 Ash content (to raw materials) (%) 0.36 ...
Embodiment 3
[0036] Weigh 30kg of fatty alcohol polyoxyethylene ether, 75kg of sodium bisulfite, 25kg of sodium hexametaphosphate, 15kg of oxalic acid, and 15kg of citric acid, and mix the above components uniformly at room temperature for 60 minutes to obtain the finished hydrolysis aid. It can leave the factory after discharging and bagging.
[0037] Self-provided masson pine wood chips, the analysis shows that the hemicellulose content is 8.65%, the ash content is 0.43%, and the lignin content is 28.52%. It was prehydrolyzed with hydrochloric acid, and the results are shown in Table 3.
[0038] Table 3 Contents of chemical components of tablets after prehydrolysis
[0039] Auxiliary dosage ( %) 0.0 0.5 0.7 1.0 Hemicellulose content (to raw material) (%) 4.87 4.16 3.87 3.65 Hemicellulose removal rate (to raw material) (%) 43.70 51.91 55.26 57.80 Ash content (to raw material) (%) 0.34 0.30 0.24 0.21 Ash remov...
PUM
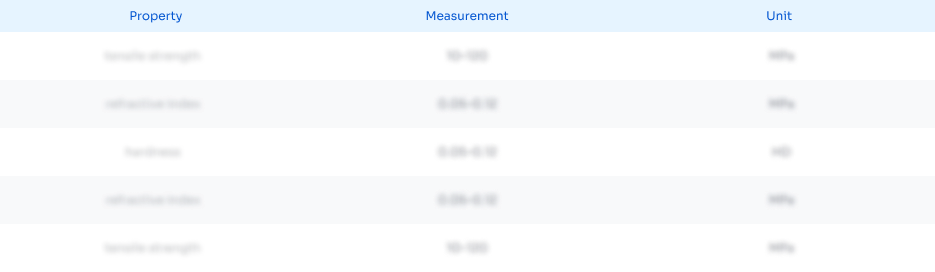
Abstract
Description
Claims
Application Information

- R&D Engineer
- R&D Manager
- IP Professional
- Industry Leading Data Capabilities
- Powerful AI technology
- Patent DNA Extraction
Browse by: Latest US Patents, China's latest patents, Technical Efficacy Thesaurus, Application Domain, Technology Topic, Popular Technical Reports.
© 2024 PatSnap. All rights reserved.Legal|Privacy policy|Modern Slavery Act Transparency Statement|Sitemap|About US| Contact US: help@patsnap.com